-
4
- #1
Things have been a little slow around here lately for my liking. In an attempt to liven things up, I'm attempting something experimental: an engineering contest with a cash prize of $150 USD. This is your chance to:
A) Earn yourself some KootBucks and;
B) Establish yourself as a GSEL (Goddam Structural Engineering Legend).
THE CHALLENGE
In the spirit of times, develop a scheme for the fabrication of a steel joist that would be fabricated on site rather than by a conventional joist supplier (Vulcraft, Canam, etc).
THE RULES
1) Include sketches or be forever disparaged.
2) Describe the benefits of your proposal as you see them.
3) Submissions will be accepted until midnight on June 5th, Pacific Time.
4) On June 6th, voting will commence.
5) Voting will close at midnight on June 12th, Pacific Time
5) Votes will be cast by way of members visiting the thread and writing a quick note to indicate their favorite scheme.
6) Votes will NOT be cast by way of giving out little purple stars. Give out all the little purple stars that you wish but none will be recorded as a formal vote.
7) Anyone may enter the contest and win the prize. However, you need to have received at least 9 little purple stars on this forum in the past in order to qualify as a judge and cast a vote that will be counted. I'm setting this restriction only as an attempt to prevent this thing from spiraling into some weird, spammy, cheating affair. Basically, if you're to be in charge of awarding the KootBucks, you need a reputation.
8) The prize will be awarded in the form of an Amazon eGift card. The winner will need to send their burner email address to my burner address or whatever. We're smart kids, we'll figure it out.
9) No prize will be awarded if there are not at least five entries to choose from, including my own.
10) If JAE shows up to judge, he can cast my vote along with his own.
May the best engineer win!
A) Earn yourself some KootBucks and;
B) Establish yourself as a GSEL (Goddam Structural Engineering Legend).
THE CHALLENGE
In the spirit of times, develop a scheme for the fabrication of a steel joist that would be fabricated on site rather than by a conventional joist supplier (Vulcraft, Canam, etc).
THE RULES
1) Include sketches or be forever disparaged.
2) Describe the benefits of your proposal as you see them.
3) Submissions will be accepted until midnight on June 5th, Pacific Time.
4) On June 6th, voting will commence.
5) Voting will close at midnight on June 12th, Pacific Time
5) Votes will be cast by way of members visiting the thread and writing a quick note to indicate their favorite scheme.
6) Votes will NOT be cast by way of giving out little purple stars. Give out all the little purple stars that you wish but none will be recorded as a formal vote.
7) Anyone may enter the contest and win the prize. However, you need to have received at least 9 little purple stars on this forum in the past in order to qualify as a judge and cast a vote that will be counted. I'm setting this restriction only as an attempt to prevent this thing from spiraling into some weird, spammy, cheating affair. Basically, if you're to be in charge of awarding the KootBucks, you need a reputation.
8) The prize will be awarded in the form of an Amazon eGift card. The winner will need to send their burner email address to my burner address or whatever. We're smart kids, we'll figure it out.
9) No prize will be awarded if there are not at least five entries to choose from, including my own.
10) If JAE shows up to judge, he can cast my vote along with his own.
May the best engineer win!
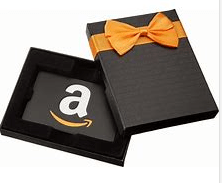