EIJPN
Electrical
- Aug 5, 2022
- 4
I want to stack some parts on top of each other. These are 17 discs, 75mm in diameter, made from 0.2mm thick aluminum sheets.
The problem is that the sheets are not totally flat, and when stacked on top of each other there are small gaps between them that can be seen when looking at the stack of sheets from the side.
I need to make sure there are no gaps between the sheets, and each sheet sits flush against the sheets above and below. To solve this problem, I am thinking of having sheets made with holes in them that I can put screws through, and then tighten bolts on the screws to clamp the sheets together.
I want to minimize the number of screws I need to use, but I want to make sure there are no gaps between the stacked sheets.
I have included an image of the 75mm diameter part with some possible places for the holes and the screws. (Holes are numbered 1-25)
Can anyone suggest where it would be best to locate the screws, and how many might be needed? Should the holes be located somewhere else?
Note, the hole for the screws is 1.2mm diameter, and the head of the screw is 2mm - if this is too small, please comment.
The problem is that the sheets are not totally flat, and when stacked on top of each other there are small gaps between them that can be seen when looking at the stack of sheets from the side.
I need to make sure there are no gaps between the sheets, and each sheet sits flush against the sheets above and below. To solve this problem, I am thinking of having sheets made with holes in them that I can put screws through, and then tighten bolts on the screws to clamp the sheets together.
I want to minimize the number of screws I need to use, but I want to make sure there are no gaps between the stacked sheets.
I have included an image of the 75mm diameter part with some possible places for the holes and the screws. (Holes are numbered 1-25)
Can anyone suggest where it would be best to locate the screws, and how many might be needed? Should the holes be located somewhere else?
Note, the hole for the screws is 1.2mm diameter, and the head of the screw is 2mm - if this is too small, please comment.
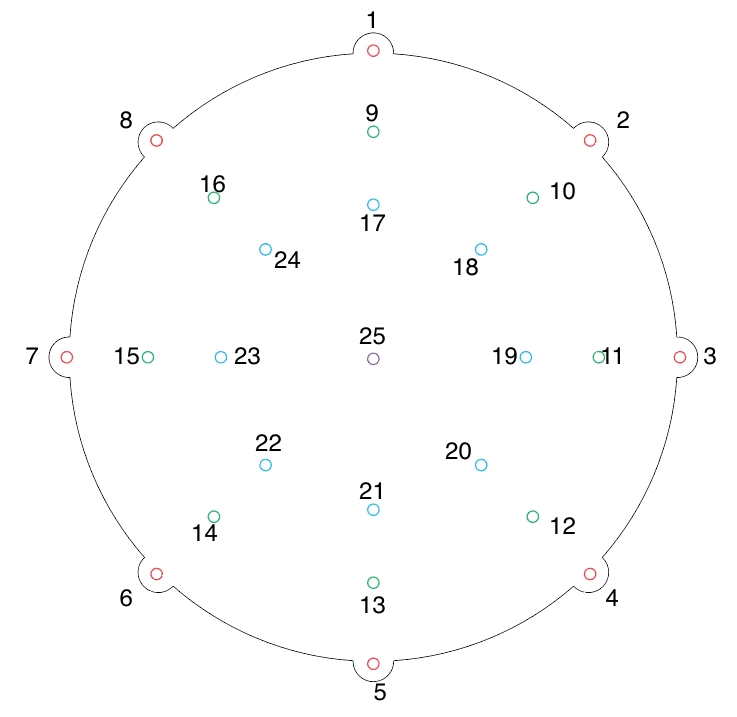