Hello,
First time posting on here. I'm working on a drawing with a group of holes that I want to control as a pattern using composite position. In the feature control box, the goal of the second line is to control the pattern's parallelism to the two datum holes. Is this the correct way of doing such or would it be something like A | B-C in the feature control box?? The actual part I am working on is not a simple rectangular shape, rather something a little more complex but I figured this was good enough to get my point across. I know I could add another datum to say, the top of the part and have parallelism to that but was wondering if I could do the same thing using composite position.
First time posting on here. I'm working on a drawing with a group of holes that I want to control as a pattern using composite position. In the feature control box, the goal of the second line is to control the pattern's parallelism to the two datum holes. Is this the correct way of doing such or would it be something like A | B-C in the feature control box?? The actual part I am working on is not a simple rectangular shape, rather something a little more complex but I figured this was good enough to get my point across. I know I could add another datum to say, the top of the part and have parallelism to that but was wondering if I could do the same thing using composite position.
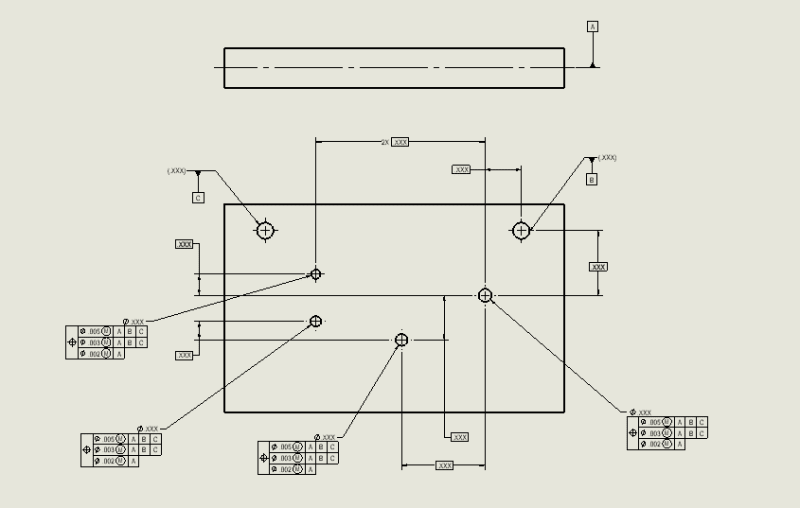