SeasonLee
Mechanical
- Sep 15, 2008
- 918
Its a simple part per ASME Y14.5, and I know its not allowed to label a center line as a datum feature, so I am confused on how to setup the part for inspection, what will you do? Its not a good print, any comments are welcome.
Season
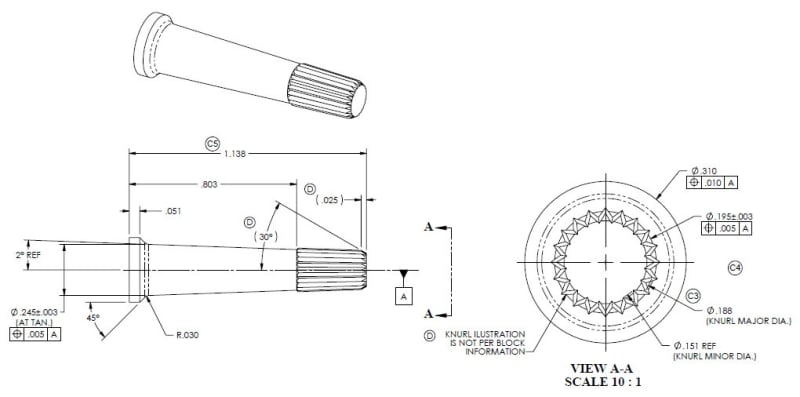
Season