pyromech
Mechanical
- Jul 30, 2008
- 39
Folks
I am reading Alex Krulikowski workbook, Exercise 5-51 and there is a mistake on Line J, datum shift. It should be 0.2;
VC=10.3-0.2=10.1
MMC-VC= 10.3-10.1=0.2
What do you think? I get annoyed when he mentions that for assembly stacks, it requires two different stacks where the components are assembled at their extremes for what you looking for. But for most cases, you can use the same stack specially in this case??
So what would be the Max Distance X? My results are attached..
thanks
I am reading Alex Krulikowski workbook, Exercise 5-51 and there is a mistake on Line J, datum shift. It should be 0.2;
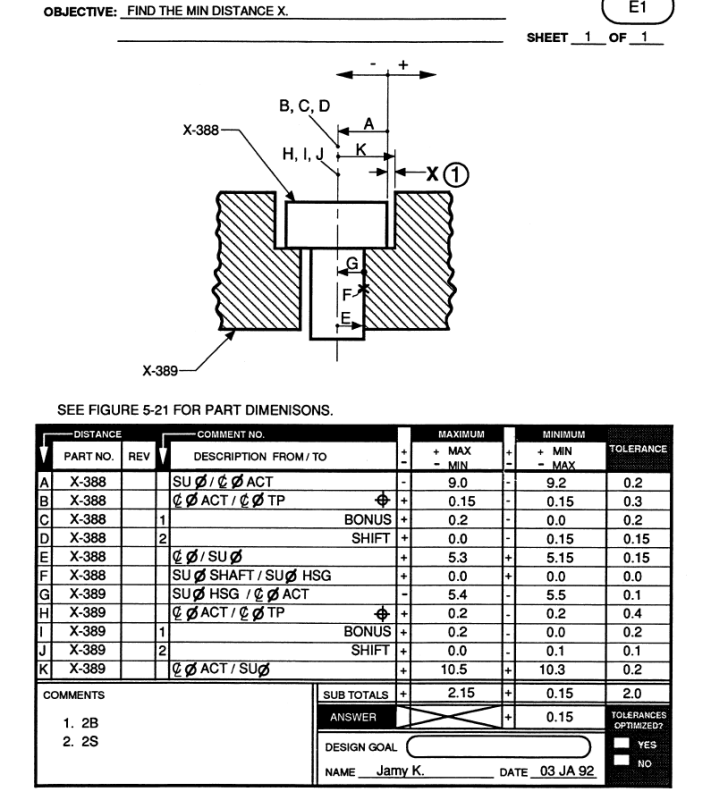
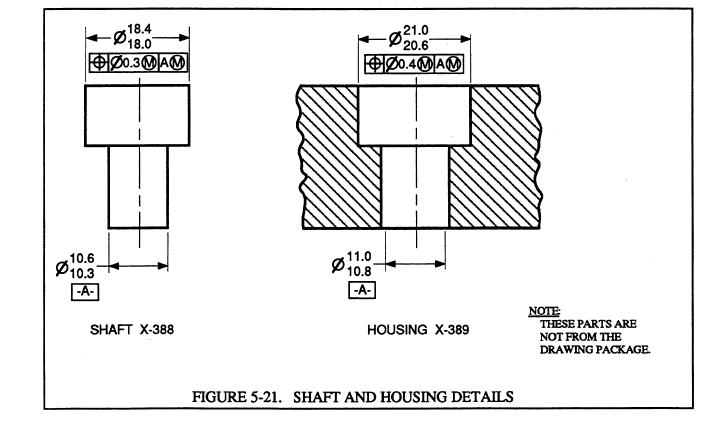
VC=10.3-0.2=10.1
MMC-VC= 10.3-10.1=0.2
What do you think? I get annoyed when he mentions that for assembly stacks, it requires two different stacks where the components are assembled at their extremes for what you looking for. But for most cases, you can use the same stack specially in this case??
So what would be the Max Distance X? My results are attached..
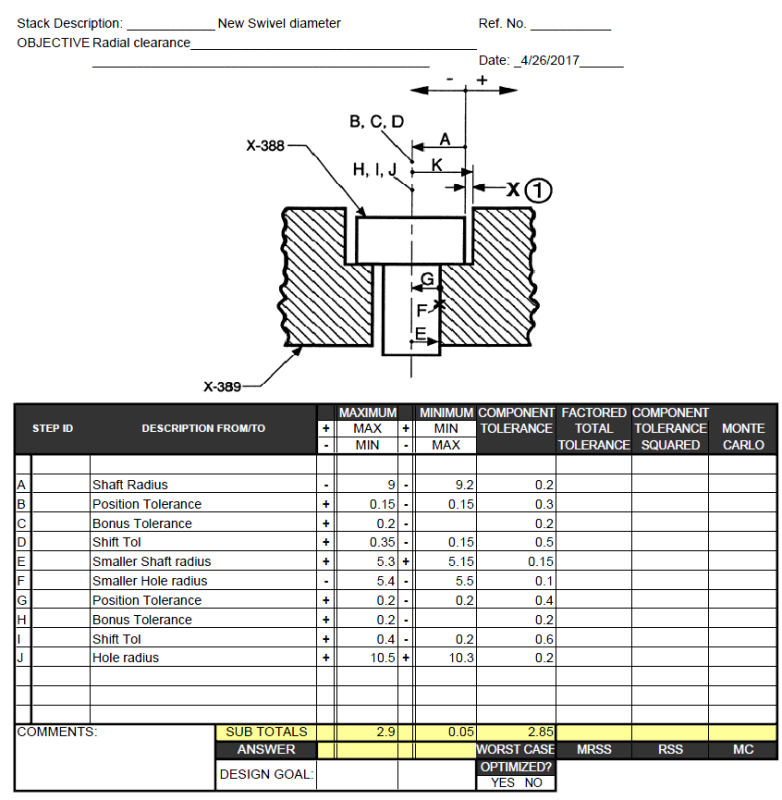
thanks