Hi, Apologies this is a very basic question.
I have a small machined part. Is it ok to choose relatively small (and separated) surfaces as the primary and secondary datum. I could choose the base of the part as the primary datum but I am reluctant because it is unimportant for the function. It would possibly easier for inspection though? The primary datum will be brazed to a mating part and the secondary surface will mate to seals.
I have attached a cropped image. The rest of the part is about the same size again but narrower.
Alternative suggestions welcome!
I have a small machined part. Is it ok to choose relatively small (and separated) surfaces as the primary and secondary datum. I could choose the base of the part as the primary datum but I am reluctant because it is unimportant for the function. It would possibly easier for inspection though? The primary datum will be brazed to a mating part and the secondary surface will mate to seals.
I have attached a cropped image. The rest of the part is about the same size again but narrower.
Alternative suggestions welcome!
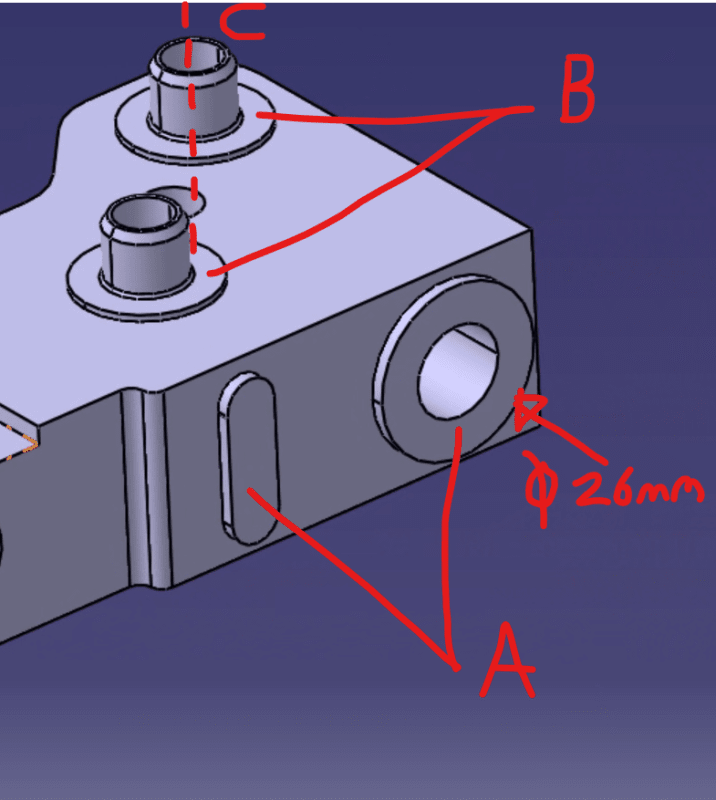