Daparojo252
Mechanical
- Mar 25, 2015
- 13
I am trying calculate the theoretical displacement of a mass that is fixed at one end, the other rigid due to a centrifugal force acting on a mass.
Where the other end is rigid, it subject to a tightening load against the application face, hence the centrifugal force, F has to overcome the force acting on the Nut due to tightening and friction to create the displacement. FF0.15.
Please see the file, and please comment if I can improve on this.
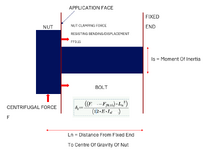
Thanks in advance.
Where the other end is rigid, it subject to a tightening load against the application face, hence the centrifugal force, F has to overcome the force acting on the Nut due to tightening and friction to create the displacement. FF0.15.
Please see the file, and please comment if I can improve on this.
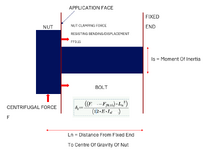
Thanks in advance.