This is a design I want to try out with a contractor on a covered pavilion project and hope to use it going forward on similar projects that are flagpoled.
Please do not respond with "Simpson has a moment base" We don't want to use that and it has limited capacity and stiffness and it needs to be set prior to placing the concrete. We also have looked at Perma Column but it has too many issues to use.
Would possibly like to substitute the bolts for a bunch of 1/4x3" Simpson SDS screws as trying to find the other side of an 8" long drilled hole is hard and they will end up wallowing it out. I am hoping bearing on the walls of the tube will be doing most of the work anyway (as long as it don't shrink too much)
Have at it...
Please do not respond with "Simpson has a moment base" We don't want to use that and it has limited capacity and stiffness and it needs to be set prior to placing the concrete. We also have looked at Perma Column but it has too many issues to use.
Would possibly like to substitute the bolts for a bunch of 1/4x3" Simpson SDS screws as trying to find the other side of an 8" long drilled hole is hard and they will end up wallowing it out. I am hoping bearing on the walls of the tube will be doing most of the work anyway (as long as it don't shrink too much)
Have at it...
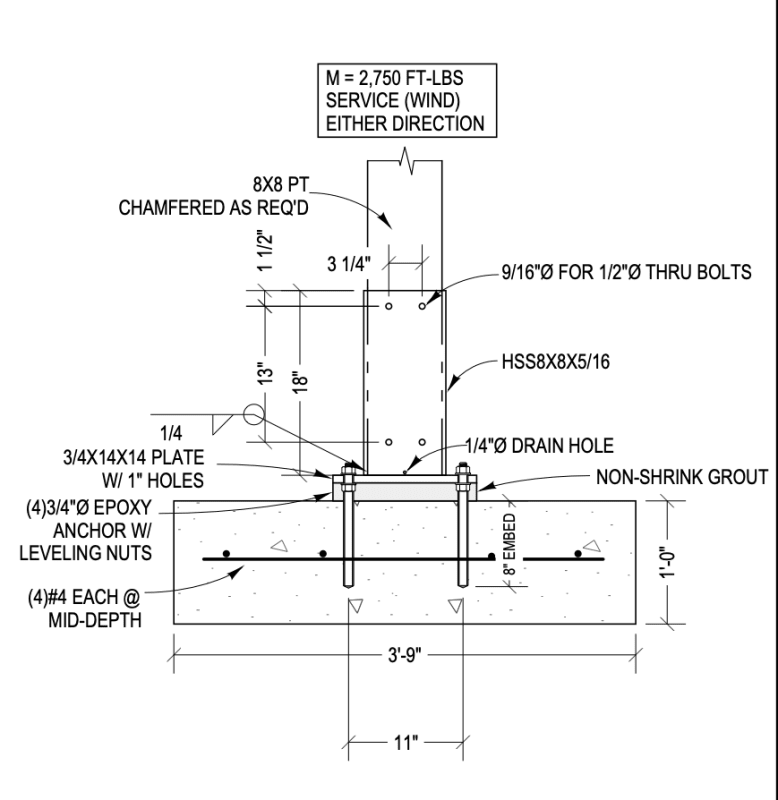