So I come here in hopes of finding a better way a lid like this.
Overall manufacturing of the lid has been successful and we haven't had any major problems.
But with the last batch, some have bent because of the welding stresses, and they cannot be restored to the final shape.
I'll try avoiding welds, but I need to redesign it, in the most simple way, using nothing else but sheet metal, and keeping the shape it has.
I was thinking of bolting to the lid, the support of the central connection. I'm not sure of this because without the "arms" the lid will become quite "flimsy".
Any ideas on how to minimally but successfully improve this?
I could go and try methods on the go, but i cannot waste any more time. I'm even asking before designing anything.
Overall manufacturing of the lid has been successful and we haven't had any major problems.
But with the last batch, some have bent because of the welding stresses, and they cannot be restored to the final shape.
I'll try avoiding welds, but I need to redesign it, in the most simple way, using nothing else but sheet metal, and keeping the shape it has.
I was thinking of bolting to the lid, the support of the central connection. I'm not sure of this because without the "arms" the lid will become quite "flimsy".
Any ideas on how to minimally but successfully improve this?
I could go and try methods on the go, but i cannot waste any more time. I'm even asking before designing anything.
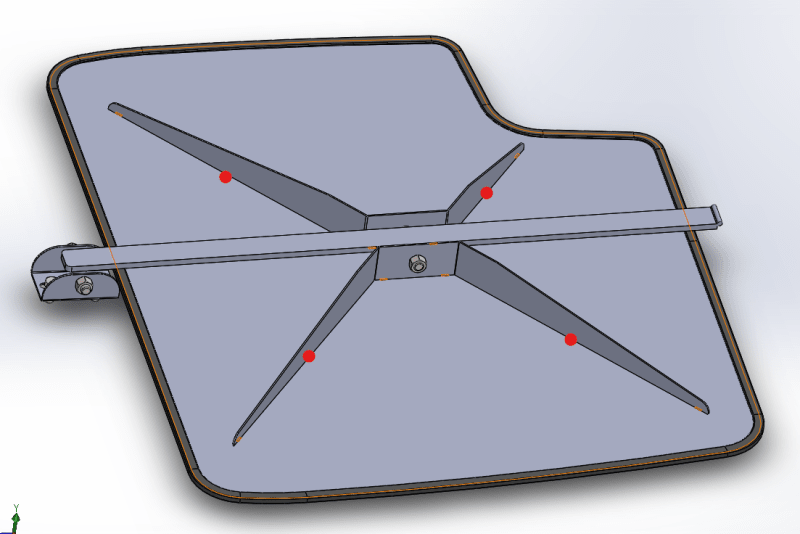
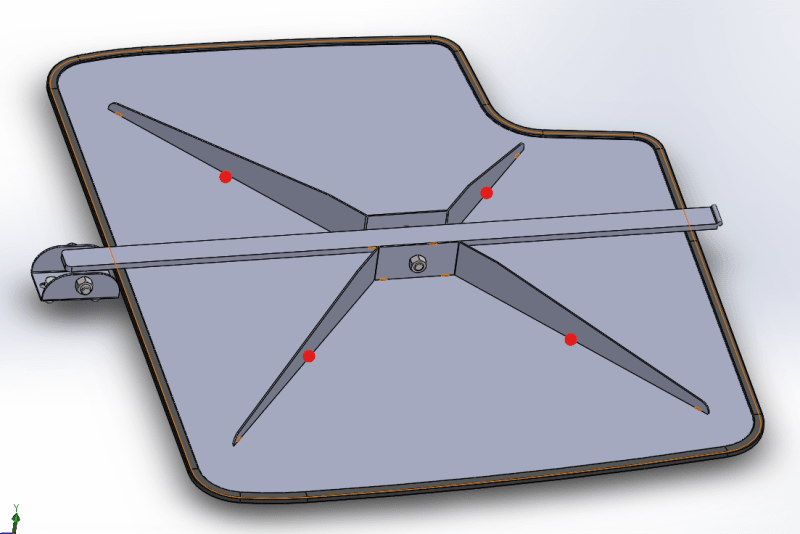
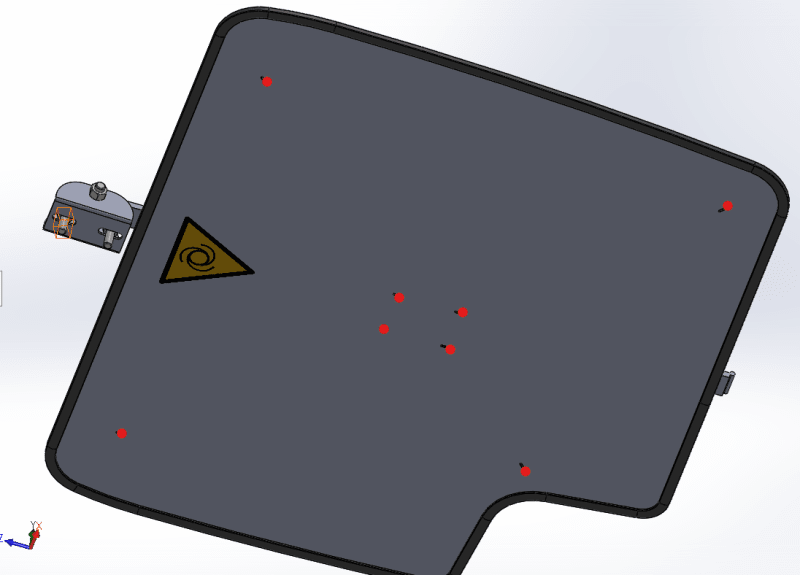