ViCH
Electrical
- Jan 9, 2020
- 74
Hi everyone. I am electrical technician, and I have problem with Emergency Diesel Generators at site. Full Power Capacity is 2.7MW, but we get speed unstable starting from 1.3 MW, if we want to give more power then engine looks like can not accelerate and frequency start to drop until under-frequency trip. We already check all fuel injection pumps, fuel pressures condition of valves, fuel filters.. Check electronic controls and all auxiliaries, but did not find any major problems.
By trending I found fuel demand is adequately changes with load requested. But I also mentioned that manifold air pressure is maintain 14.2 PSI before start, and 14 PSI +-0.3 fluctuating during and after start. Is it OK? Could it be problem with turbocharger, or wastegate control?
Engine: GE 16V228.
Turbocharger: 7S1716 compressor end. E-40811A
Viktor
Electrical Technician II
By trending I found fuel demand is adequately changes with load requested. But I also mentioned that manifold air pressure is maintain 14.2 PSI before start, and 14 PSI +-0.3 fluctuating during and after start. Is it OK? Could it be problem with turbocharger, or wastegate control?
Engine: GE 16V228.
Turbocharger: 7S1716 compressor end. E-40811A
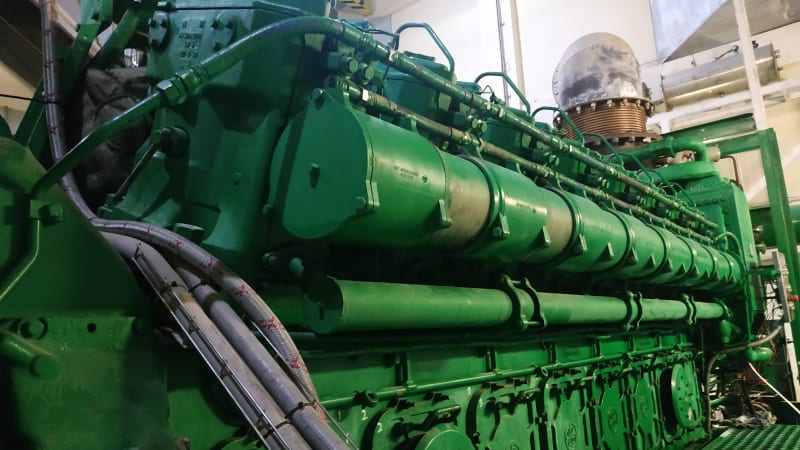
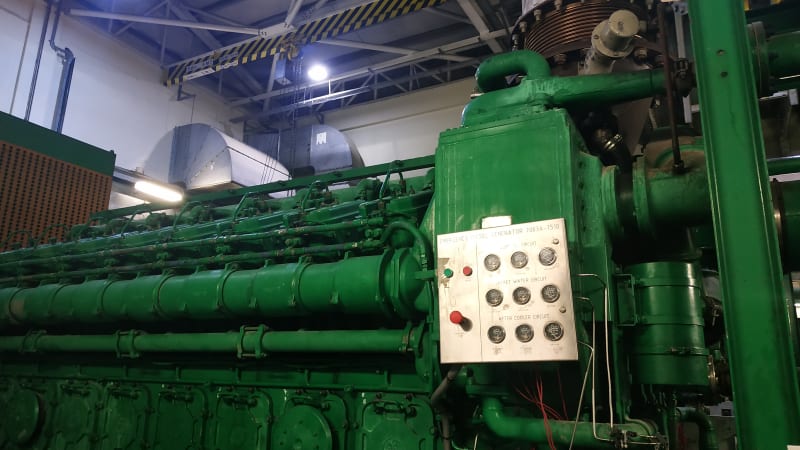
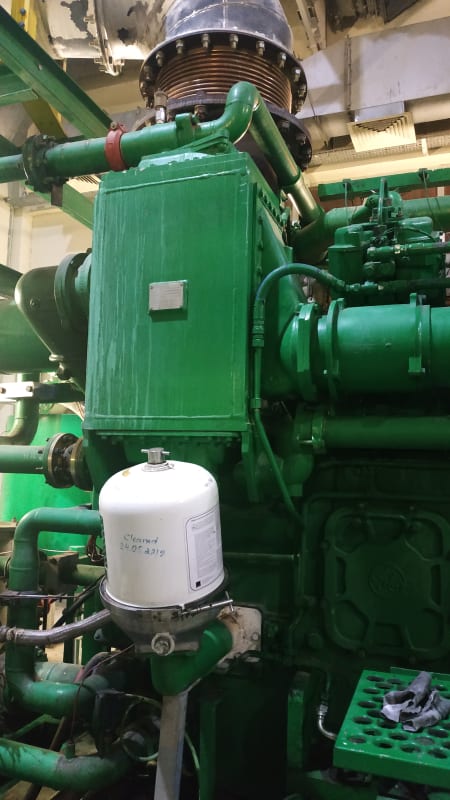
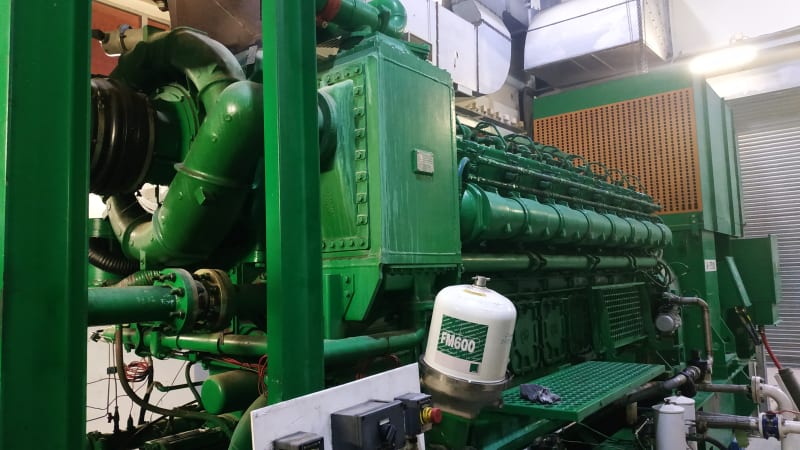
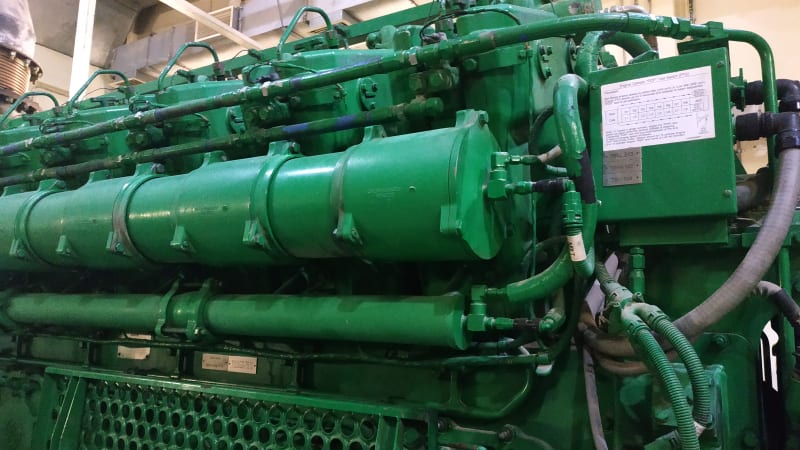
Viktor
Electrical Technician II