Vitkacy1989
Structural
Hi all,
Picture below explains the system. I have a solid model with moment load at one side and fixation at other. Two tubes are connected with two bolts to check moment transfer. F2 is obviously larger than F1 due to different levers lengths.
FEA shows high stress at bolt's shaft mainly due to bolt bending. And now I just thought, if I would calculate this connection by hand, that bolt would see no bending at all, just the stress from F2 tension. But in FEA, we get enormously higher stress due to bending alone.
Am I missing some moment at bolts in my free body diagram? Why hand calculation results and FEA are different?
Picture below explains the system. I have a solid model with moment load at one side and fixation at other. Two tubes are connected with two bolts to check moment transfer. F2 is obviously larger than F1 due to different levers lengths.
FEA shows high stress at bolt's shaft mainly due to bolt bending. And now I just thought, if I would calculate this connection by hand, that bolt would see no bending at all, just the stress from F2 tension. But in FEA, we get enormously higher stress due to bending alone.
Am I missing some moment at bolts in my free body diagram? Why hand calculation results and FEA are different?
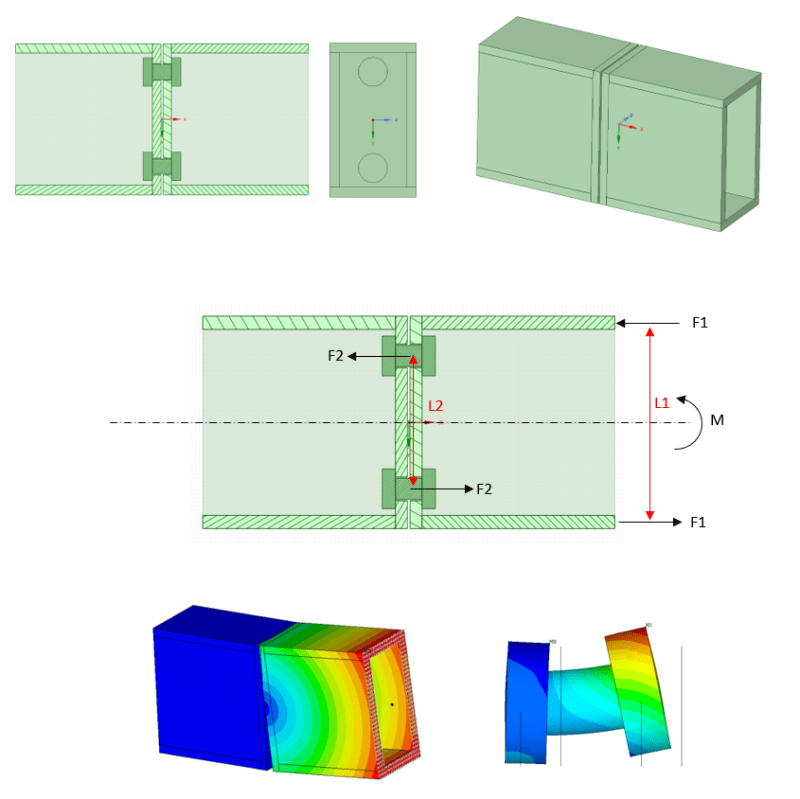