Ultganon2437
Mechanical
- Jun 19, 2021
- 8
Hi I had a question in the image below. Is that setup possible with a Long Radius 90 deg elbow? Of course the elbow would have to be cut down in order to match the degrees but the thing is that a subcontractor is saying that a Long Radius elbow will not work given the length 3-9/16" that they would need Short radius 90 elbows instead. This is entirely new to me so if someone could please explain how this works or why a long radius elbow is unable to help I would really appreciate it. I know this is more of a pipefitter question but I couldnt find any forums of pipefitters.
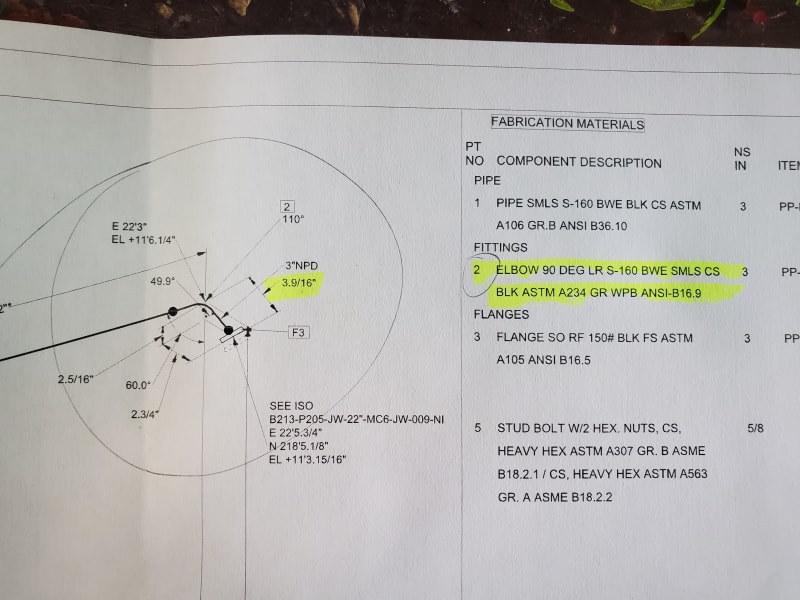