FlashPurp
Industrial
Hello,
I am working on stress on pump suction piping coming from a tank. I am seeing high moments and nozzle loads on my pump during hot and cold operation. I believe the issue is with how my header is growing and contracting during the 2 cases, so I was wondering the best way to restrain without transferring loads to the pump nozzles? Or would it be best to reroute the header to add flex and reduce movement?
Information:
Fluid: Water
Low Temp: 30 F; Hot Temp: 150 F
Design Pressure: 50 PSIG
Material: A312 TP304
Header Size: 18" SCH 10S
Branch Size: 12" SCH 10S
Nozzle Size: 8"
This is the layout I currently have it:
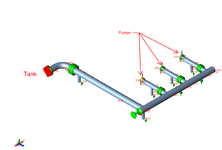
Movement during cold operation:
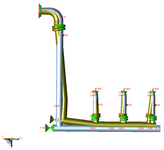
Movement during hot operation:
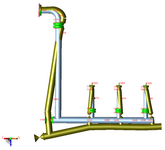
I am working on stress on pump suction piping coming from a tank. I am seeing high moments and nozzle loads on my pump during hot and cold operation. I believe the issue is with how my header is growing and contracting during the 2 cases, so I was wondering the best way to restrain without transferring loads to the pump nozzles? Or would it be best to reroute the header to add flex and reduce movement?
Information:
Fluid: Water
Low Temp: 30 F; Hot Temp: 150 F
Design Pressure: 50 PSIG
Material: A312 TP304
Header Size: 18" SCH 10S
Branch Size: 12" SCH 10S
Nozzle Size: 8"
This is the layout I currently have it:
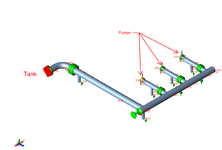
Movement during cold operation:
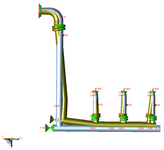
Movement during hot operation:
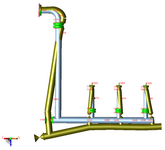