Rat5
Agricultural
- Aug 6, 2016
- 29
What are those small deck ridges ? ( bmw f1 engine 1500cc 1200hp)
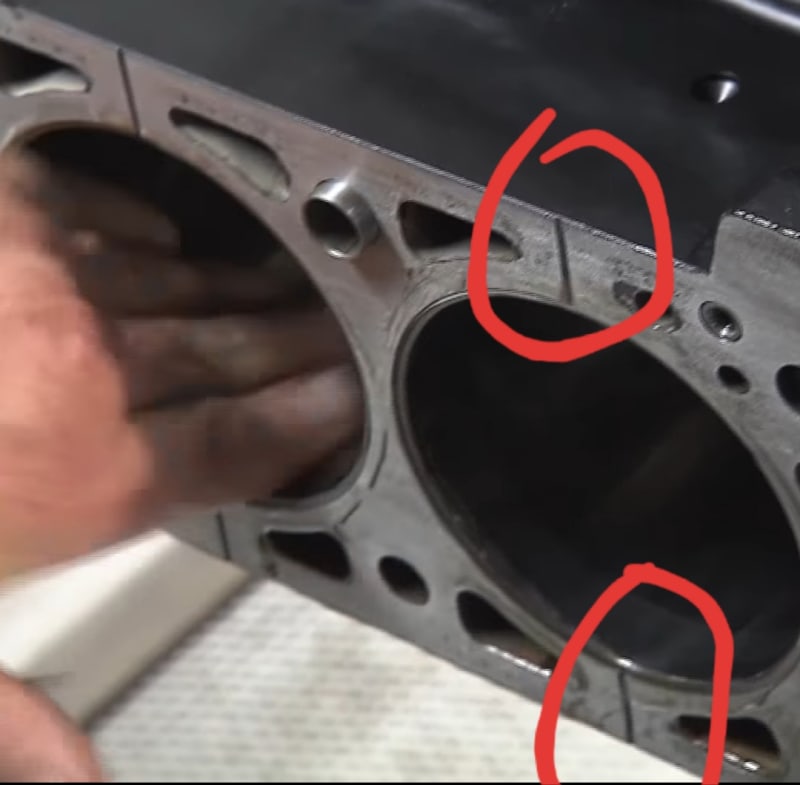
Follow along with the video below to see how to install our site as a web app on your home screen.
Note: This feature may not be available in some browsers.
gruntguru said:The counterbored cylinder can only be to accommodate a metal o-ring - the M12 gasket in the above link would not work.