innominata
Bioengineer
How much does it matter where the fasteners are placed on an o-ring face seal?
Park O Ring handbook doesn't say anything about it. I'm currently using a racetrack groove. I've made the radius of the groove curvature 3x the diameter of the o-ring but I worry about where I've placed the screw holes.
The enclosure material will be injection moulded polycarbonate with the groove using either an NBR or FKM o-ring.
I can understand that the fasteners should be placed symmetrically but beyond that I'm not sure what the placement and spacing requirements should be or why it's not often mentioned in guides. My question is from your experience, apart from symmetry does it happen often that the placement of fasteners influences the seal in this type of application (plastic electronic enclosure)?
Park O Ring handbook doesn't say anything about it. I'm currently using a racetrack groove. I've made the radius of the groove curvature 3x the diameter of the o-ring but I worry about where I've placed the screw holes.
The enclosure material will be injection moulded polycarbonate with the groove using either an NBR or FKM o-ring.
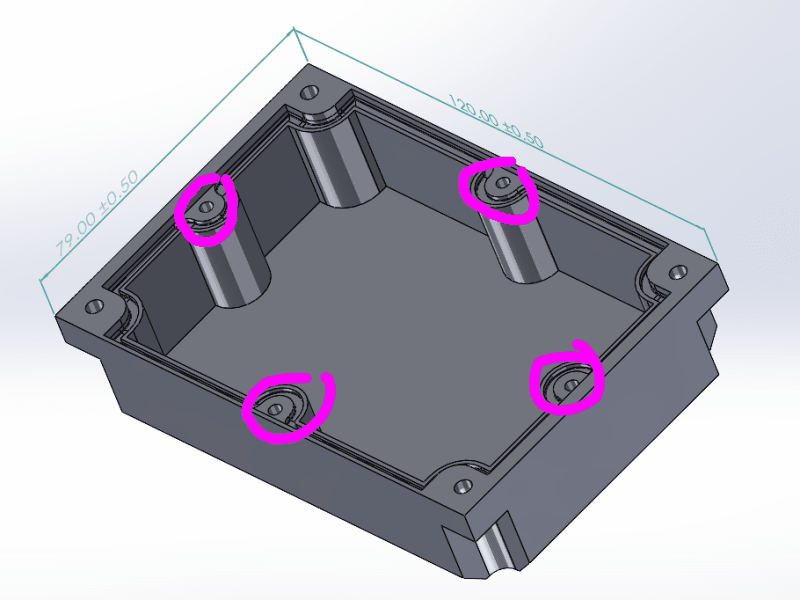
I can understand that the fasteners should be placed symmetrically but beyond that I'm not sure what the placement and spacing requirements should be or why it's not often mentioned in guides. My question is from your experience, apart from symmetry does it happen often that the placement of fasteners influences the seal in this type of application (plastic electronic enclosure)?