KootK
Structural
- Oct 16, 2001
- 18,573
I've got a precast column corbel in a parking garage with a required fire rating of 3HRS. And I'm interested in the fire rating requirements for:
1) The beam bearing plates on the corbel below and, more so;
2) The primary corbel rebar welded to the bearing plates which, somewhat by definition, doesn't have a ton of cover.
I assume that there's some "out" for not having to fireproof the bearing plates but I'm unsure about the corbel reinforcing. Do I need to use 2" bearing plates just to get the rebar cover for 3HR? Does that even make sense given that any heat on the exposed bearing plate is likely to transmit that heat straight to the rebar anyhow?
Rationally, I feel that these element do not need to be fire rated the same way that primary members do because the odds of fire getting to and locally taxing these elements seems unlikely. That said, I'd like to see an exclusion in the codes rather than making this stuff up myself. Does anybody know of such an exclusion? Or can anyone confirm that I'm out to lunch in thinking that such an exclusion exists?
1) The beam bearing plates on the corbel below and, more so;
2) The primary corbel rebar welded to the bearing plates which, somewhat by definition, doesn't have a ton of cover.
I assume that there's some "out" for not having to fireproof the bearing plates but I'm unsure about the corbel reinforcing. Do I need to use 2" bearing plates just to get the rebar cover for 3HR? Does that even make sense given that any heat on the exposed bearing plate is likely to transmit that heat straight to the rebar anyhow?
Rationally, I feel that these element do not need to be fire rated the same way that primary members do because the odds of fire getting to and locally taxing these elements seems unlikely. That said, I'd like to see an exclusion in the codes rather than making this stuff up myself. Does anybody know of such an exclusion? Or can anyone confirm that I'm out to lunch in thinking that such an exclusion exists?
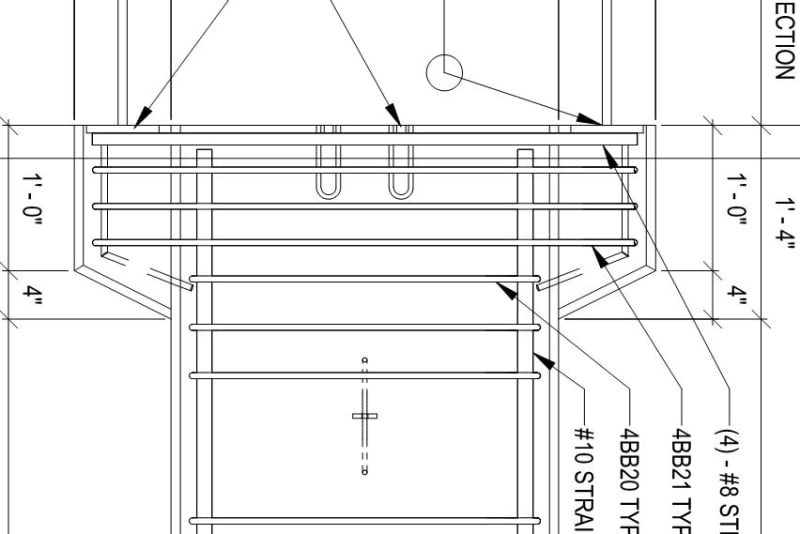