I have to fix a steel console into existing RC beam. Console is supporting a steel canopy beam.
Since RC beam is 250/300 mm I m very limited about how to destribute anchors. I have to consider minimum edge spacing from the edge of concrete and between anchors. So I came up with this:
Normally Id use more than single line of anchors, but in this case forces are small so I think it is OK. Calculations shows that 2 anchors are more than sufficient bu I still feel somewhat uneasy because I have only a single line of anchors. Id add another line but since RC beam is only 300 mm high, I have a problem with steel beam since it shouldnt be too high above the RC beam.
Since RC beam is 250/300 mm I m very limited about how to destribute anchors. I have to consider minimum edge spacing from the edge of concrete and between anchors. So I came up with this:
Normally Id use more than single line of anchors, but in this case forces are small so I think it is OK. Calculations shows that 2 anchors are more than sufficient bu I still feel somewhat uneasy because I have only a single line of anchors. Id add another line but since RC beam is only 300 mm high, I have a problem with steel beam since it shouldnt be too high above the RC beam.
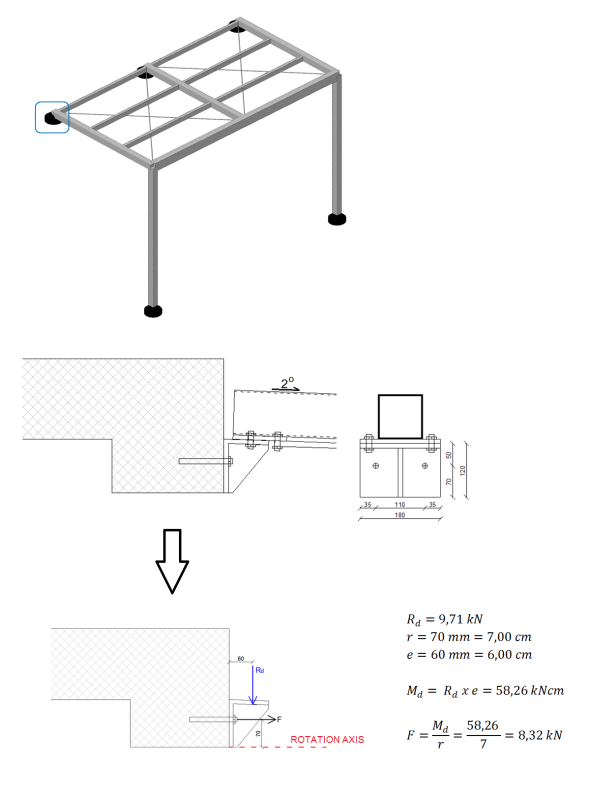