Jack Benson
Industrial
Hello,
We are developing a heat recovery device for domestic hot water (grey water not black water).
The heat exchanger is made of 304 steel.
At the moment, we use PVC connections to the 2 inlets / 2 outlets to ensure there is no contact with copper or brass fittings.
I would like to change some of these to steel parts. They can be 303, 304 or 316 steel.
The reason for the PVC connectors connected to the heat exchanger is to prevent galvanic corrosion.
Is there any risk of galvanic corrosion if we connect this flexible steel tube directly to the heat exchanger: (I work for a French start up - your browser should translate).
Other fittings I have seen contain 316 or 316L steel. Would these be suitable?
Does the L (Low Carbon) change the risk of experiencing galvanic corrosion?
I have seen tables such as this:
I have also read this thread:
Any help would be appreciated.
thank-you
Jack
We are developing a heat recovery device for domestic hot water (grey water not black water).
The heat exchanger is made of 304 steel.
At the moment, we use PVC connections to the 2 inlets / 2 outlets to ensure there is no contact with copper or brass fittings.
I would like to change some of these to steel parts. They can be 303, 304 or 316 steel.
The reason for the PVC connectors connected to the heat exchanger is to prevent galvanic corrosion.
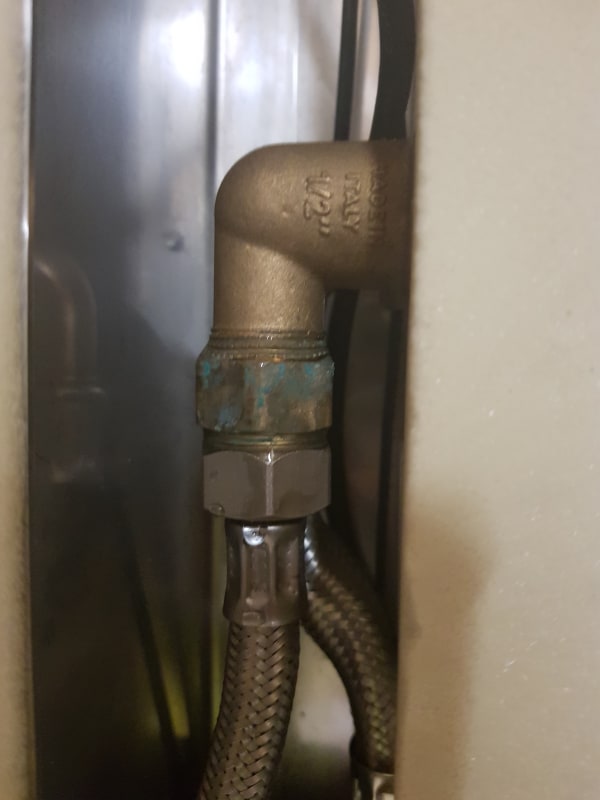
Is there any risk of galvanic corrosion if we connect this flexible steel tube directly to the heat exchanger: (I work for a French start up - your browser should translate).
Other fittings I have seen contain 316 or 316L steel. Would these be suitable?
Does the L (Low Carbon) change the risk of experiencing galvanic corrosion?
I have seen tables such as this:
I have also read this thread:
Any help would be appreciated.
thank-you
Jack