CheckerHater
Mechanical
In recent discussion thread1103-442213 we opened Costco-sized can of worms regarding use of orientation controls.
Here is the question I wanted to ask but had a feeling that it would hijack the thread, add confusion to the discussion and not get as much attention as (in my opinion) it deserves.
I would like to collect opinions of members of the community to the problem:
How would you approach the case of angularity applied to surface randomly oriented wrt your coordinate system / DRF as shown on the picture?
"For every expert there is an equal and opposite expert"
Arthur C. Clarke Profiles of the future
Here is the question I wanted to ask but had a feeling that it would hijack the thread, add confusion to the discussion and not get as much attention as (in my opinion) it deserves.
I would like to collect opinions of members of the community to the problem:
How would you approach the case of angularity applied to surface randomly oriented wrt your coordinate system / DRF as shown on the picture?
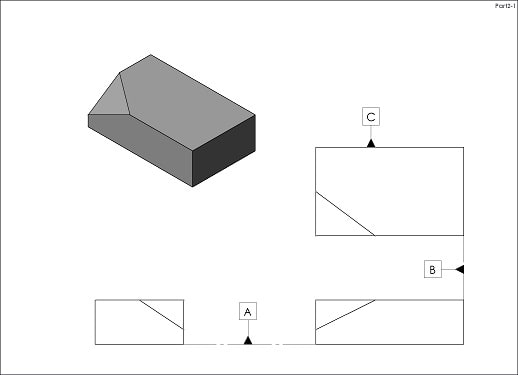
"For every expert there is an equal and opposite expert"
Arthur C. Clarke Profiles of the future