Rwelch9
Mechanical
- Apr 22, 2020
- 116
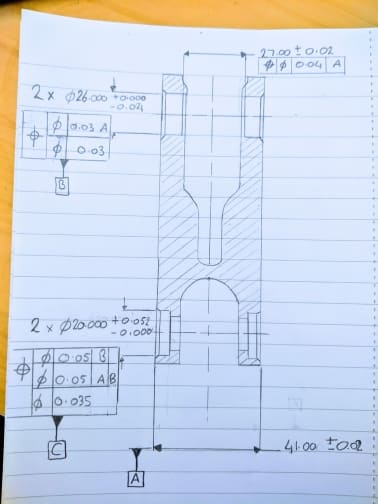
Hi guys,
Can anyone point out any flaws you see with these call outs on this drawing.
The idea is the best way to control and dimensions 4 Cylindrical pockets / with the front and back being as close as coaxial as possible.
Thanks
Ross