ElCidCampeador
Mechanical
Hi,
my client is contesting me a vessel that I built (pressure vessel acc. to ASME VIII Div.1) because he is not able to connect correctly it to his piping line.
Here below what my client has measured (different height gap about 3mm):
I ask you if it's possible to fix it by pullings tie rod of flange with a different torque depending of the position of bolts, so that flanges will have a side more compressed than the other (reducing this gap).
Thank you
my client is contesting me a vessel that I built (pressure vessel acc. to ASME VIII Div.1) because he is not able to connect correctly it to his piping line.
Here below what my client has measured (different height gap about 3mm):
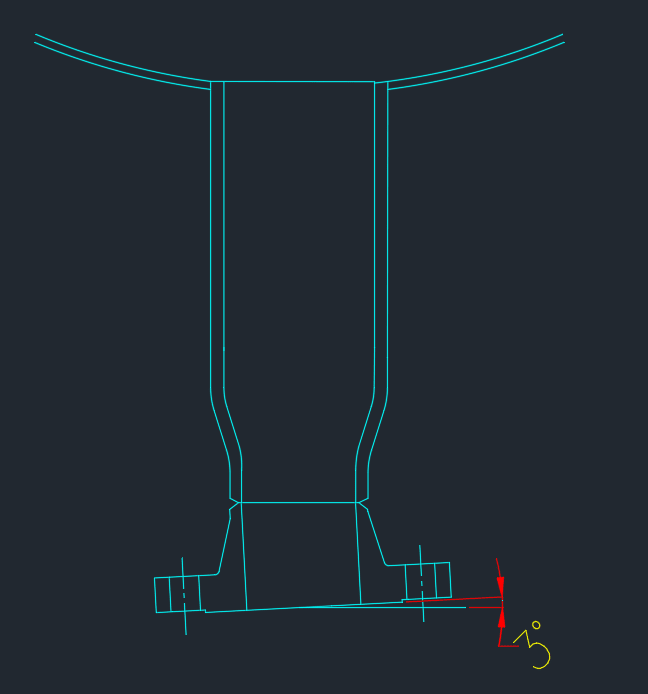
I ask you if it's possible to fix it by pullings tie rod of flange with a different torque depending of the position of bolts, so that flanges will have a side more compressed than the other (reducing this gap).
Thank you