free_flyer
Aerospace
- Aug 16, 2020
- 7
My design has a linear, sliding 'cassette' [purple] which slides by pulling on the teflon cable [yellow]
In the cassette are magnets (x15) which attract to a mating part (not shown) with the same number of magnets but with reversed poles.
When the cassette is in the closed position, the magnets attract and hold the mating part.
When the cassette is in the open position, the magnets repel and eject the mating part.
In terms of magnetics, when the cassette is in the closed position the force required to slide the cassette open is known as the 'shear' force, whereas the force between the mating parts is known as the 'axial' force..
I have a working prototype, but I am trying to reduce the shear force required to slide the cassette to the open position (i.e. to eject the mating part)
Currently (when the cassette is in the closed position) the shear force to slide open the cassette is around 6 to 7 kg and the axial force between the mating parts is about 10kg.
Ideally I want the axial force to be as large as possible (when the cassette is in the closed position) yet the shear force to be as small as possible.
Below is a top view showing the cassette in the closed position...
Below is a top view showing the cassette in the open position...
The distance the cassette moves is around 12mm (i.e. between the open and closed position).
I've been trying to think of a way to decrease the shear force to slide the cassette open, without having a detrimental effect on the axial force (such as creating an air gap between the mating magnets).
Originally the cassette ran on linear bearings and rails, but these made little or no difference to the shear force so I removed them.
I then looked into something like a rack and pinion (does this even give a gearing advantage?)and other kinds of gear and cam mechanisms, but I've made no progress.
How can I reduce the shear force to slide the cassette open and preferably without increasing the size of the design too much ?
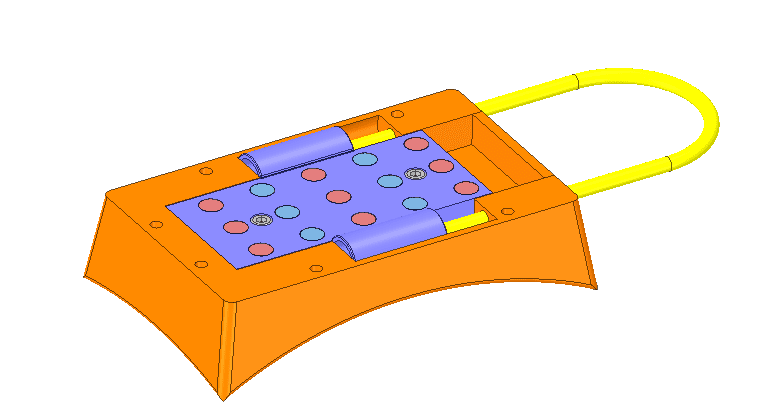
In the cassette are magnets (x15) which attract to a mating part (not shown) with the same number of magnets but with reversed poles.
When the cassette is in the closed position, the magnets attract and hold the mating part.
When the cassette is in the open position, the magnets repel and eject the mating part.
In terms of magnetics, when the cassette is in the closed position the force required to slide the cassette open is known as the 'shear' force, whereas the force between the mating parts is known as the 'axial' force..
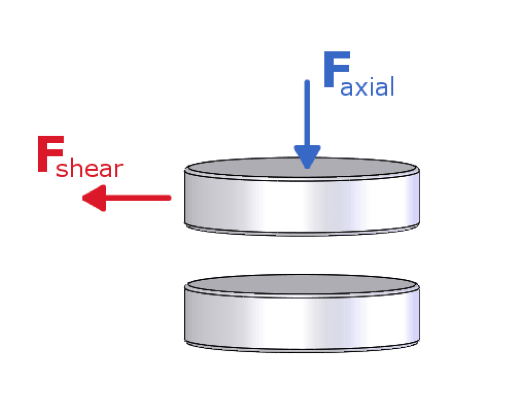
I have a working prototype, but I am trying to reduce the shear force required to slide the cassette to the open position (i.e. to eject the mating part)
Currently (when the cassette is in the closed position) the shear force to slide open the cassette is around 6 to 7 kg and the axial force between the mating parts is about 10kg.
Ideally I want the axial force to be as large as possible (when the cassette is in the closed position) yet the shear force to be as small as possible.
Below is a top view showing the cassette in the closed position...
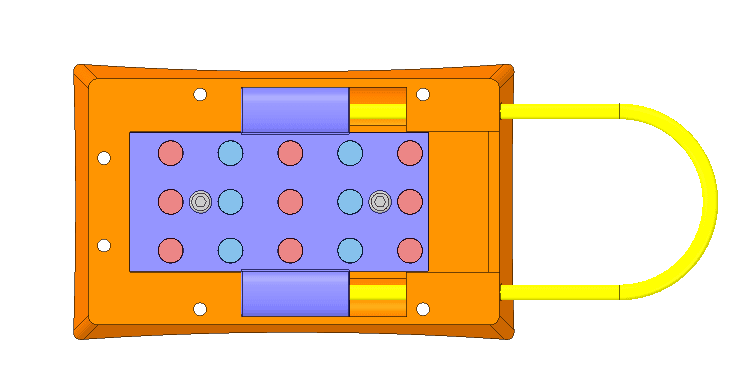
Below is a top view showing the cassette in the open position...
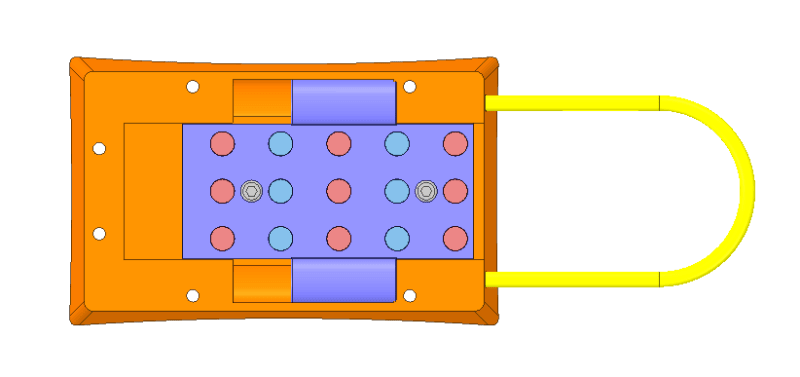
The distance the cassette moves is around 12mm (i.e. between the open and closed position).
I've been trying to think of a way to decrease the shear force to slide the cassette open, without having a detrimental effect on the axial force (such as creating an air gap between the mating magnets).
Originally the cassette ran on linear bearings and rails, but these made little or no difference to the shear force so I removed them.
I then looked into something like a rack and pinion (does this even give a gearing advantage?)and other kinds of gear and cam mechanisms, but I've made no progress.
How can I reduce the shear force to slide the cassette open and preferably without increasing the size of the design too much ?