FMPJ
Structural
- Aug 10, 2020
- 11
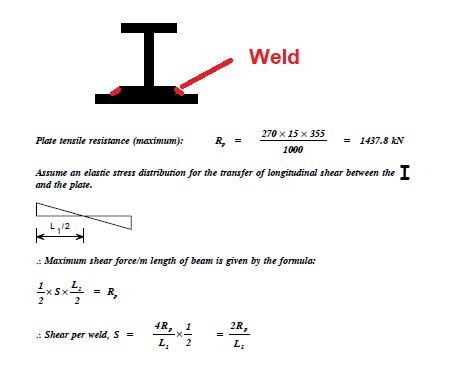
Hi Folks,
Anyone could please explain the principle shown on above screenshot.
I'd like to understand the relationship between the maximum longitudinal shear and maximum plate tensile resistance when assumed elastic distribution stress.
Thanks for your help.
Best Regards,
JPMF