Jonathan Tang
Mechanical
- Dec 5, 2020
- 5
Hi guys,
Let's say we have the assembly of three blocks placed in a container such that the worse case dimensions of the block and the inner width of the container results in zero gap. Therefore, in non-worse case situations, there will be a non-zero gap on the right side.
Question is: What methods can we use to reduce this gap further?
Any assumption on type of fit, block and container material etc is allowed.
For example, two methods are 1) Use RSS so that nominal gap can be reduce. 2) Built in interference but cool the blocks so it shrinks and heat up the container so it expands so that the blocks can fit.
I can't think of any other methods - a press fit? But not sure how that would work.
Let's say we have the assembly of three blocks placed in a container such that the worse case dimensions of the block and the inner width of the container results in zero gap. Therefore, in non-worse case situations, there will be a non-zero gap on the right side.
Question is: What methods can we use to reduce this gap further?
Any assumption on type of fit, block and container material etc is allowed.
For example, two methods are 1) Use RSS so that nominal gap can be reduce. 2) Built in interference but cool the blocks so it shrinks and heat up the container so it expands so that the blocks can fit.
I can't think of any other methods - a press fit? But not sure how that would work.
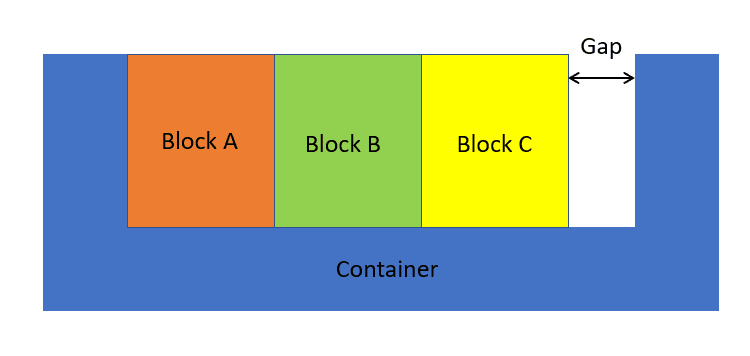