H choudhary
Mechanical
- May 20, 2023
- 10
Hi,
I am running a test on a ceiling mount monitor bracket. I have been run the job for hours now but it keeps aborting. the warning messages are negative eigenvalues. my step configuration are okay, you can see the picture, I think you'll agree. I have also checked all my BCs, interactions and material properties but still can't find the error.
Could someone please explain what exactly could be the problem and how can i tackle negative eigenvalues warnings.
any help is appreciated.
thank you
I am running a test on a ceiling mount monitor bracket. I have been run the job for hours now but it keeps aborting. the warning messages are negative eigenvalues. my step configuration are okay, you can see the picture, I think you'll agree. I have also checked all my BCs, interactions and material properties but still can't find the error.
Could someone please explain what exactly could be the problem and how can i tackle negative eigenvalues warnings.
any help is appreciated.
thank you
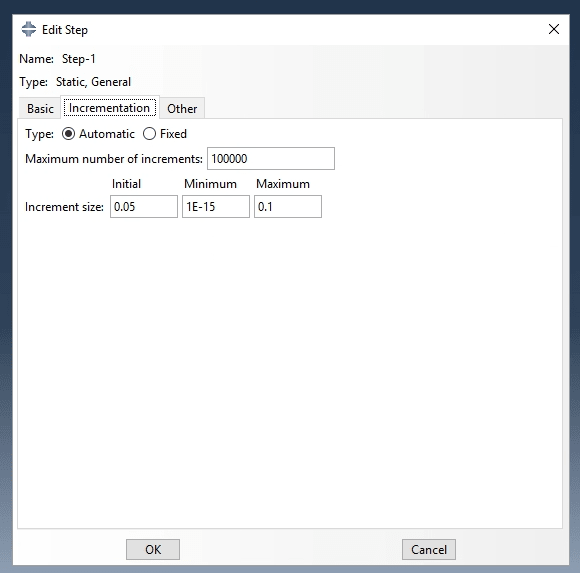
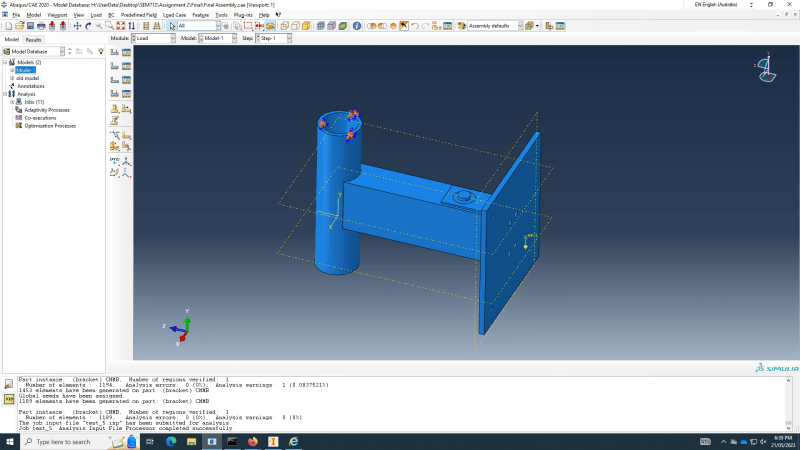
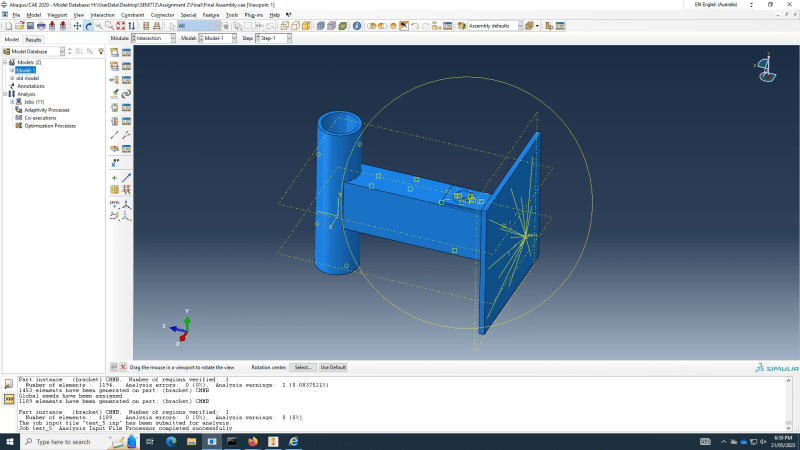
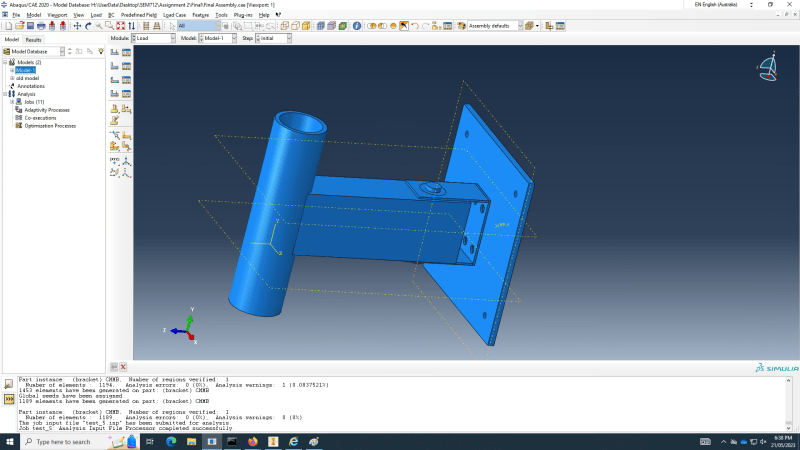