tmalik3156
Structural
Good day all.
May be this is a simple question, but we learn by asking those who know.
We are designing a steel foundation for a Bailey type bridge system. This will be a permanent bridge. The foundation consists of three piles (HP 310x 125) at each end of a pile cap (W 1000x295). The Pile cap carries load (P) of the bridge. We need stiffeners to prevent buckling of the web and distortion of the flanges of W 1000x295. Question is, what should be the orientation of the diagonal stiffeners (shown in red)? Is it like the one shown on the left, or the one on the right?
Thank you
May be this is a simple question, but we learn by asking those who know.
We are designing a steel foundation for a Bailey type bridge system. This will be a permanent bridge. The foundation consists of three piles (HP 310x 125) at each end of a pile cap (W 1000x295). The Pile cap carries load (P) of the bridge. We need stiffeners to prevent buckling of the web and distortion of the flanges of W 1000x295. Question is, what should be the orientation of the diagonal stiffeners (shown in red)? Is it like the one shown on the left, or the one on the right?
Thank you
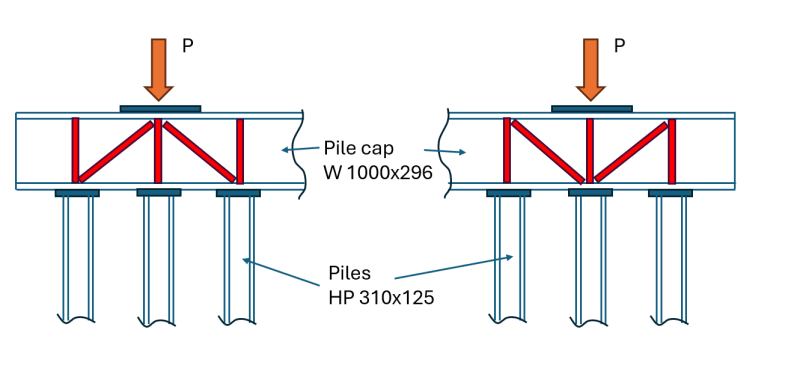