XR250
Structural
- Jan 30, 2013
- 5,953
Saw this the other day while getting some tires. The post is about 20 ft. tall and has 20 ft. span girts +/- on each side. Seems like that tiny brace from the bottom of the end frame to the purlin is pretty optimistic for transferring the out-of-plane post load into the diaphragm. Seems the purlin would not be too happy about it either.
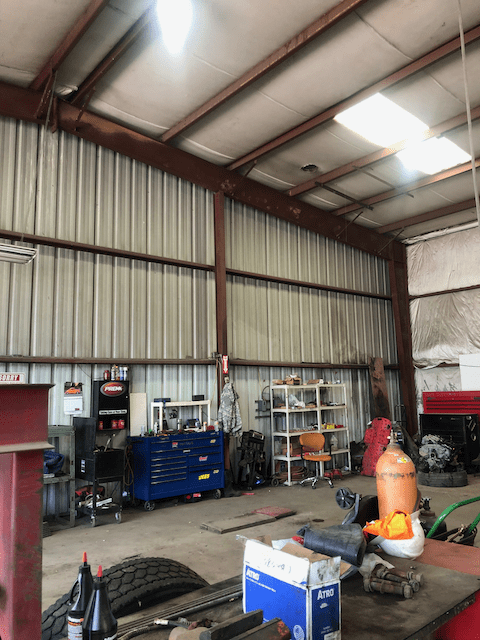