Ethnan
Electrical
- Mar 13, 2020
- 57
Hello Everyone,
I need information on how to design a PM generator and have the rotor turn freely, without too much cogging from the forces due to the strong neodymium magnet.
I have several diverging information from my research and need to be sure of what I am doing. Generally, there seems to be a relationship between the airgap, the number of poles, the pole size, the number of slots, slot size and distance between slots, for one to achieve a cogging-free generator.
Please I need some professional guidance. Any useful advice will be highly appreciated. Thank you all.
Kind Regards
I need information on how to design a PM generator and have the rotor turn freely, without too much cogging from the forces due to the strong neodymium magnet.
I have several diverging information from my research and need to be sure of what I am doing. Generally, there seems to be a relationship between the airgap, the number of poles, the pole size, the number of slots, slot size and distance between slots, for one to achieve a cogging-free generator.
Please I need some professional guidance. Any useful advice will be highly appreciated. Thank you all.
Kind Regards
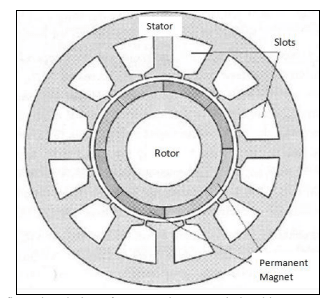