SeizeTheMoment
Structural
- Sep 16, 2020
- 36
Per AISC table J2.5, fillet welds in holes and slots are allowed in tension and is allowed to be neglected in design. However, plug and slot welds are not allowed to be designed in tension/compression. I'm having a hard time visualizing this. If a plug/slot weld was used, would it not be able to support a tension load and have a failure plane similar to a fillet weld? The way I see it, a plug/slot weld would fill up the entire hole while a fillet weld only at the edges - how will the fillet weld be able to support the axial loads with less weld, while a plug/slot weld which fills the entire hole cannot?
Don't bend to the stress, seize the moment!
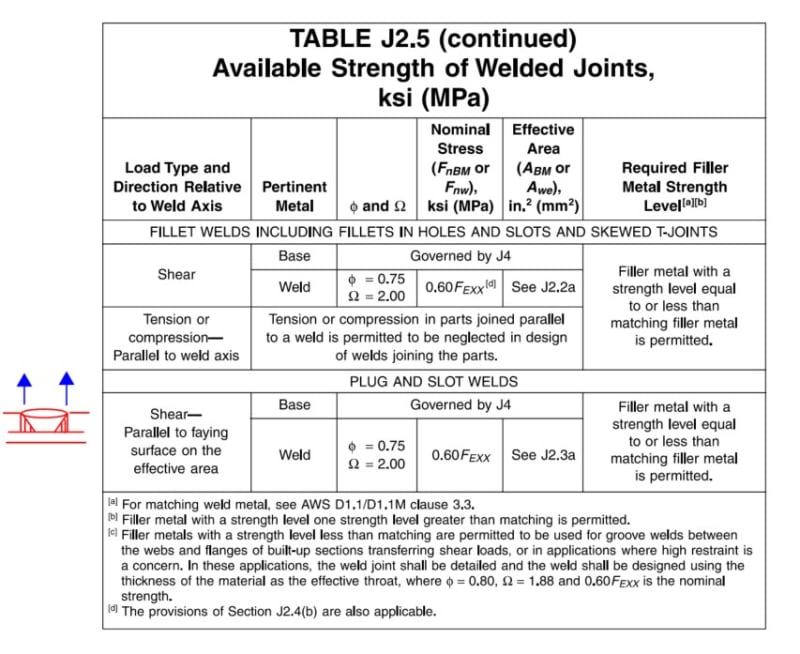
Don't bend to the stress, seize the moment!