tlwhite0311
Mechanical
- Jan 4, 2018
- 8
I came across this tolerancing scheme that struck me as odd. There is a position tolerance on a circular face where a conical feature has been faced off (dare I say a spot face?). I thought that you cannot control anything that is not a feature of size (i.e. with two opposing points anywhere along the feature) with Position. I spoke to an inspector and he sounded a bit confused when I mentioned opposing points, he said he could find the position of the face by generating lines on the CMM from the face of the cone and then those lines would generate points where they intersected the face, he could then use those to find the position of the face. I have never used a CMM yet so I don't know anything about that, but I wanted to get another opinion. See image for reference, the left is the top view, the right is the front view.
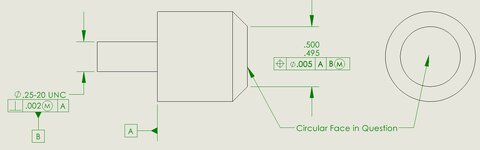
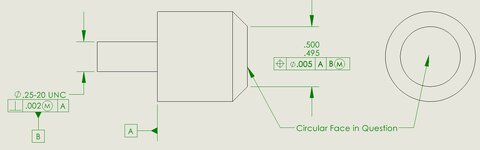