Quentin Nguyen
Industrial
- Apr 20, 2023
- 14
Dear Engineers,
I am running into a problem finding or calculating Yield Stress (MPa) and Ultimate Tensile Stress (MPa) for SUS310S and SUS316 using ASME Section II Part D to match the table as attached.
I am running FEA based on ASME Section VIII Div.2 Part 5.3.3 - Elastic-Plastic Analysis for a Heat Exchanger. Mechanical Datasheet as shown in the photo below.
Although, can anyone please show me why SUS310S yield and tensile are larger than SUS316 because based on my calculation using ASME II D, SUS310S yield and tensile shall be smaller than SUS316?
Thank you so much!
Regards!
I am running into a problem finding or calculating Yield Stress (MPa) and Ultimate Tensile Stress (MPa) for SUS310S and SUS316 using ASME Section II Part D to match the table as attached.
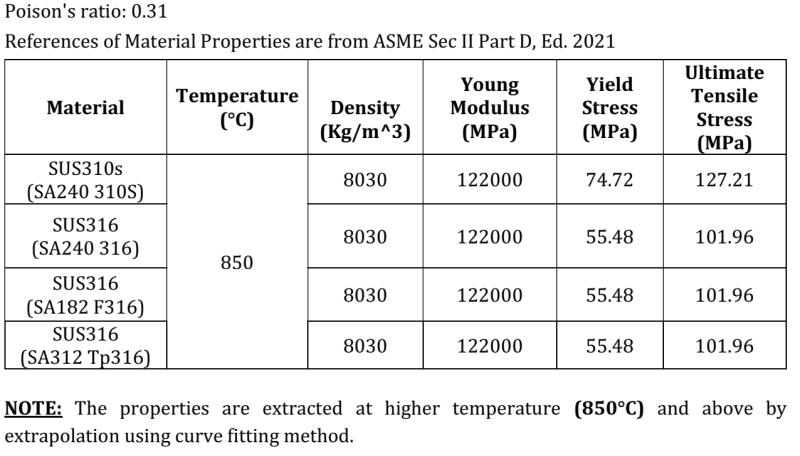
I am running FEA based on ASME Section VIII Div.2 Part 5.3.3 - Elastic-Plastic Analysis for a Heat Exchanger. Mechanical Datasheet as shown in the photo below.
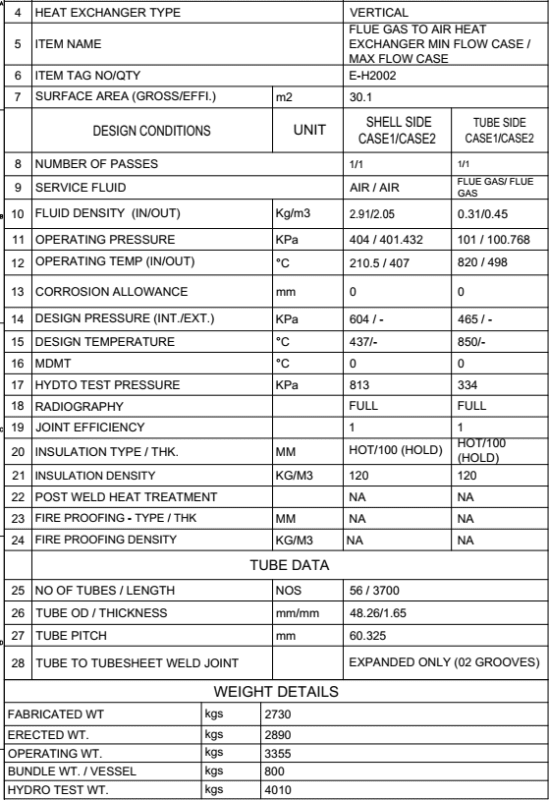
Although, can anyone please show me why SUS310S yield and tensile are larger than SUS316 because based on my calculation using ASME II D, SUS310S yield and tensile shall be smaller than SUS316?
Thank you so much!
Regards!