heli_eng28
New member
- Nov 1, 2019
- 7
There's a bit of a debate in the office regarding dimensioning drawings. We bounce around back and forth between how drawings are dimensioned. Sometimes it's dependent on which machinist will be manufacturing the part, sometimes it depends on the manufacturing method, and sometimes it depends on the what the engineer ate for breakfast. One of our older engineers doesn't even know how to create a proper dimensioned drawing and forwards everything to us.
We DO NOT use GD&T currently. I've tried applying some dimensioning guidelines from GT&D, but I'll get kickback from the machinists on certain parts/dimensioning schemes about having to calculate dimensions, among other complaints.
A lot of the older drawings use hidden lines and we've been moving away from that. Some guys want them, some don't. Is there a standard on that? Some guys complain about dimensions on the part, others don't. Is it okay to have dimensions on parts?
Some guys like hole to hole dimensions, others like dimensions off a common datum so they don't have to calculate anything. I guess that's dependent on the design intent of the part and what dimension you're trying to hold exactly.
I've attached two drawings. Is either one more correct than the other?
This document is a bit more advanced then some of the others I've come across online and covers a good bit of information:
Are there any others like this that are more advanced?
We DO NOT use GD&T currently. I've tried applying some dimensioning guidelines from GT&D, but I'll get kickback from the machinists on certain parts/dimensioning schemes about having to calculate dimensions, among other complaints.
A lot of the older drawings use hidden lines and we've been moving away from that. Some guys want them, some don't. Is there a standard on that? Some guys complain about dimensions on the part, others don't. Is it okay to have dimensions on parts?
Some guys like hole to hole dimensions, others like dimensions off a common datum so they don't have to calculate anything. I guess that's dependent on the design intent of the part and what dimension you're trying to hold exactly.
I've attached two drawings. Is either one more correct than the other?

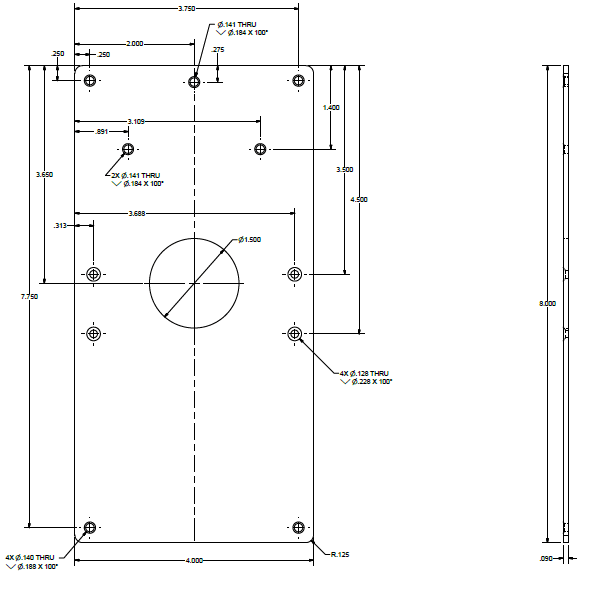
This document is a bit more advanced then some of the others I've come across online and covers a good bit of information:
Are there any others like this that are more advanced?