-
1
- #1
kurtz
Mechanical
- Sep 10, 2016
- 34
Please look at the picture. Is it necessary to assume any other force from opening the safety valve?
I've seen some people add force directly at the outlet of the safety valve.
I've seen some people add force directly at the outlet of the safety valve.
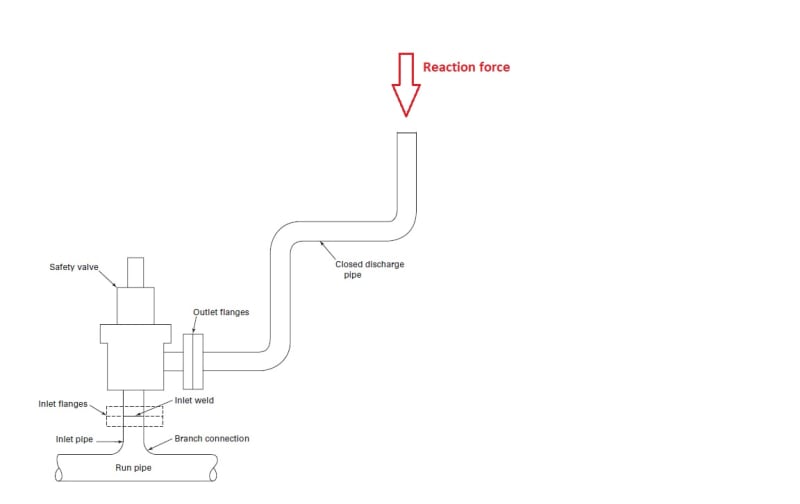