struggle66
Civil/Environmental
- Jul 5, 2013
- 127
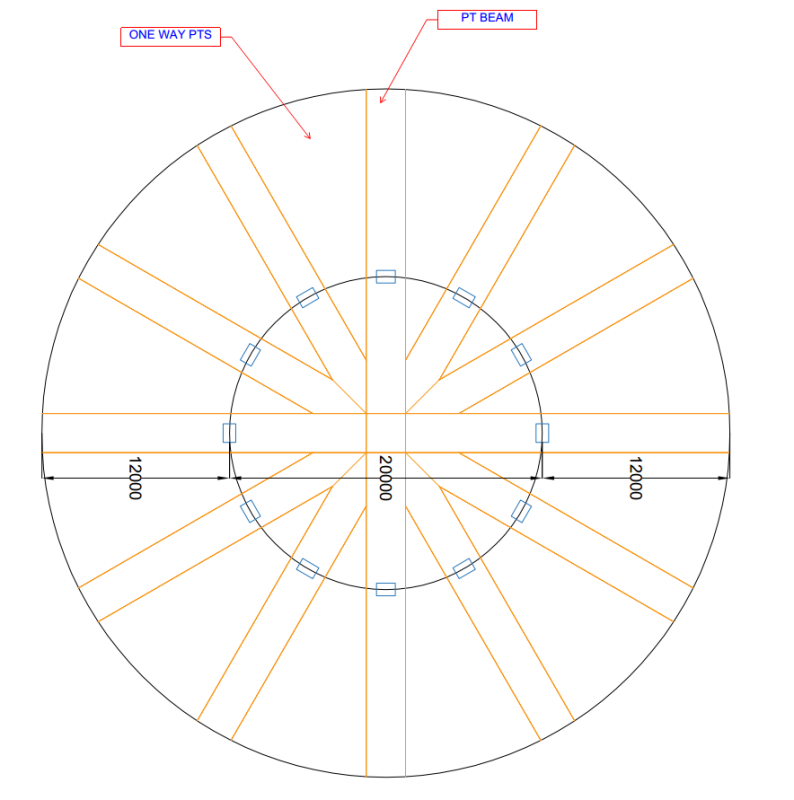
Hi Good Day Everyone,
I've got to propose PT layout for above circular PT layout for a residential building with 12m cantilever on each side (Columns are only allowed on inner circle perimeter). I am thinking to propose as above but if that so except the rebar & tendon congestion @ the center of the circle, there will be a lot of pre-compression (P/A) due to PT & a lot beam design will share the section. It is my first time to encounter this kind of layout.
How should I approach, analysis & design? Thanks in advance for your help.
Thanks