kellez
Civil/Environmental
- Nov 5, 2011
- 276
Hello everyone, I am designing a 3.5m high retaining wall of which 2.0m will be covered by infill soil. see picture attached
I have specified a layer of bitumen felt to be applied on the wall up to 2.2m high.
Next on top of the bitumen felt i have specified the installation of a geodrain membrane.
Do you guys think i will also need to specify additives to the concrete such as crystalline waterproofing?
Regards
I have specified a layer of bitumen felt to be applied on the wall up to 2.2m high.
Next on top of the bitumen felt i have specified the installation of a geodrain membrane.
Do you guys think i will also need to specify additives to the concrete such as crystalline waterproofing?
Regards
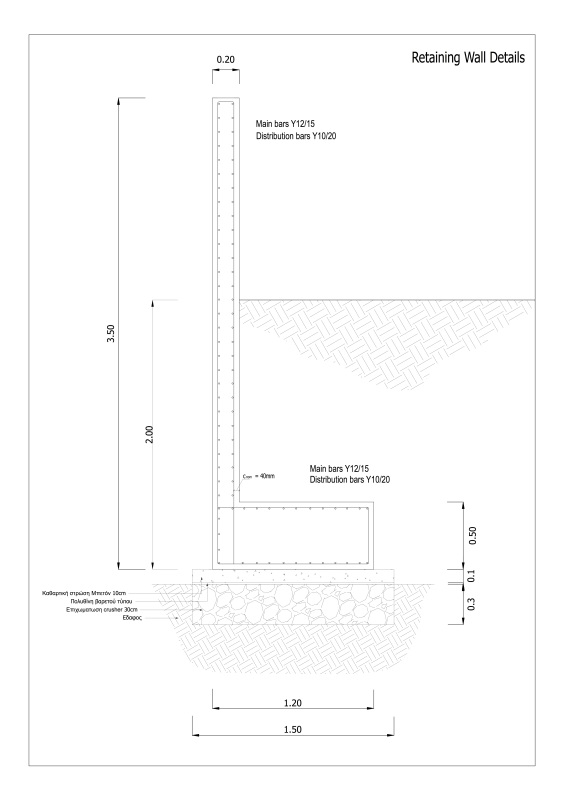