ALK2415
Structural
- Sep 15, 2014
- 289
What's your opinions on following lack of QC/QA control of major highway bridge ?
can you estimate actual reduction percentage of bearing capacity of these curved box girder ?
Is there a reliable testing method that could investigate the propagated corrosions among rebars ?
Can loading test (actual loaded trucks HS20-44) prevail "corrosion" and its effects on short terms structural performance
can you estimate actual reduction percentage of bearing capacity of these curved box girder ?
Is there a reliable testing method that could investigate the propagated corrosions among rebars ?
Can loading test (actual loaded trucks HS20-44) prevail "corrosion" and its effects on short terms structural performance
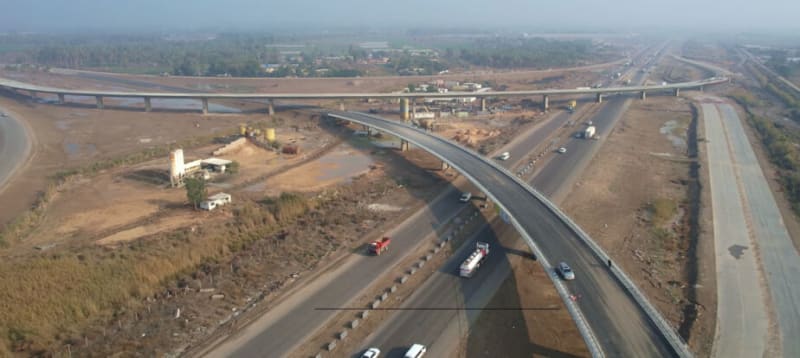
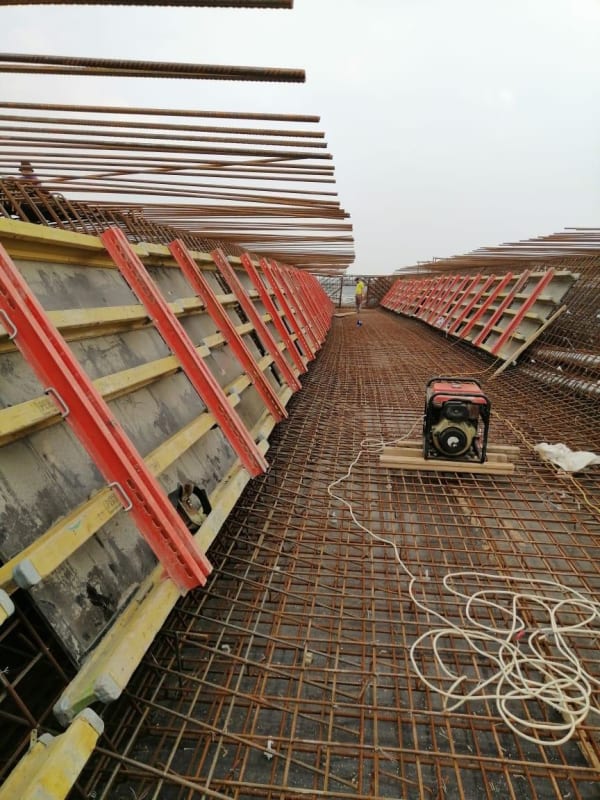
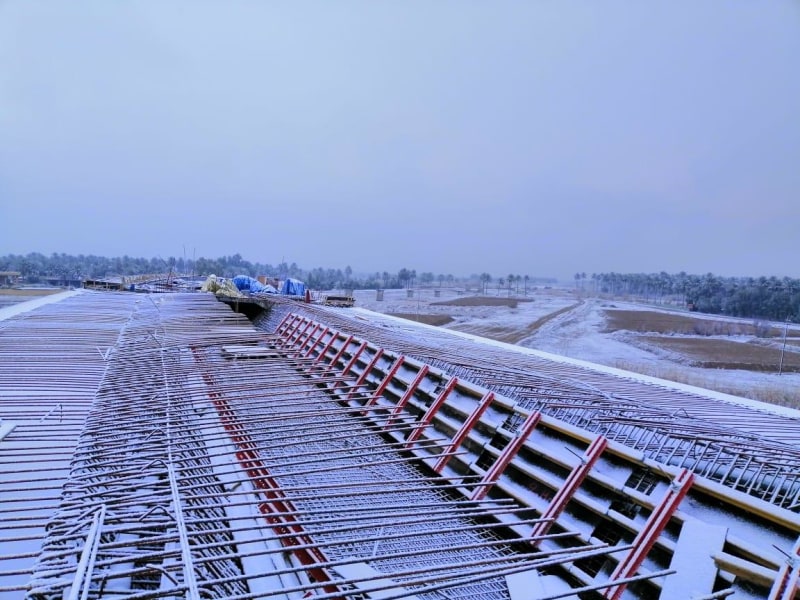
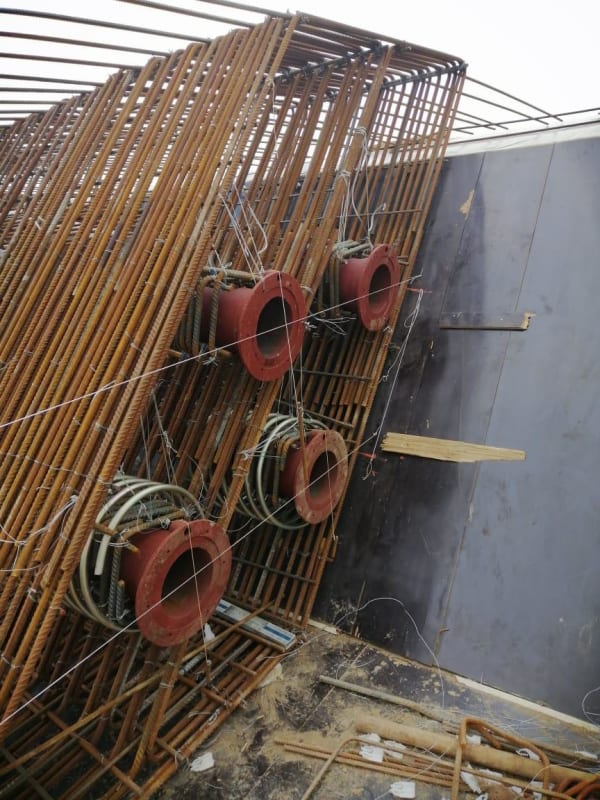
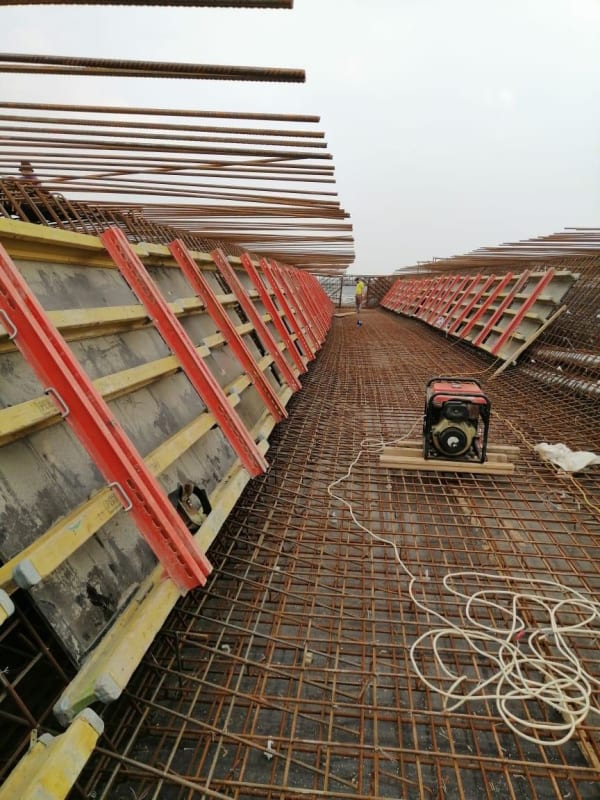
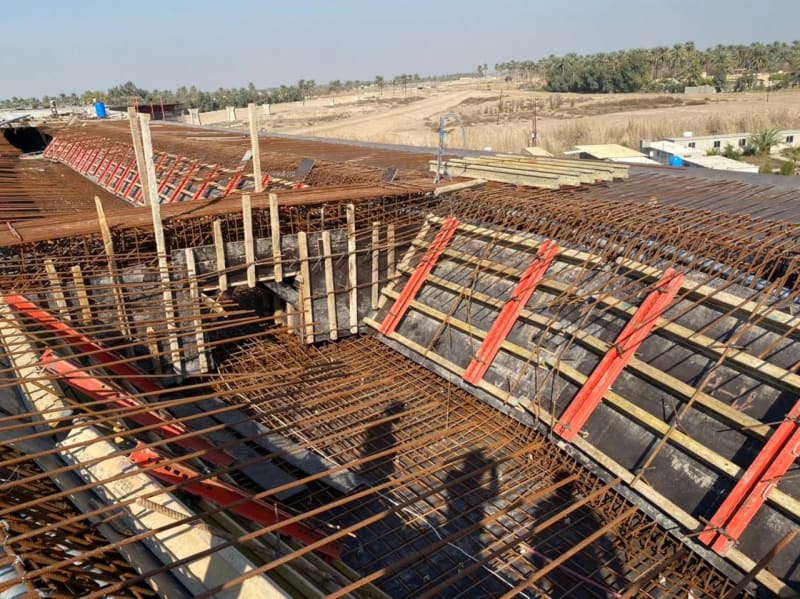
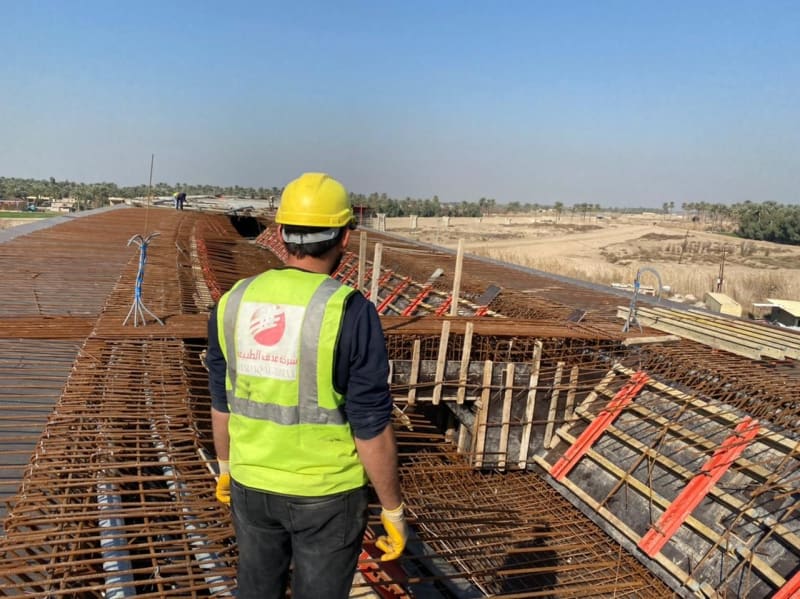