Have a river pump with a motor.
The motor is 440vAC, 60hz, 100hp, 134A , 3-phase. rated to output 2,045cubic/meter/min of water.
It's tripping its protection quickly and repeatedly.
It's also delivering 20% more water than expected, (2,454cubic/meter/min).
My take is that the twenty percent is pulling 20% more power hence the trips.
My advice is to restrict the outlet to reduce the mass-flow.
Now seeing the pictures finally, it shows the pump is an axial propeller type. Can I restrict the flow on this type and reduce the loading? Is a propeller a centrifugal pump?
Keith Cress
kcress -
The motor is 440vAC, 60hz, 100hp, 134A , 3-phase. rated to output 2,045cubic/meter/min of water.
It's tripping its protection quickly and repeatedly.
It's also delivering 20% more water than expected, (2,454cubic/meter/min).
My take is that the twenty percent is pulling 20% more power hence the trips.
My advice is to restrict the outlet to reduce the mass-flow.
Now seeing the pictures finally, it shows the pump is an axial propeller type. Can I restrict the flow on this type and reduce the loading? Is a propeller a centrifugal pump?
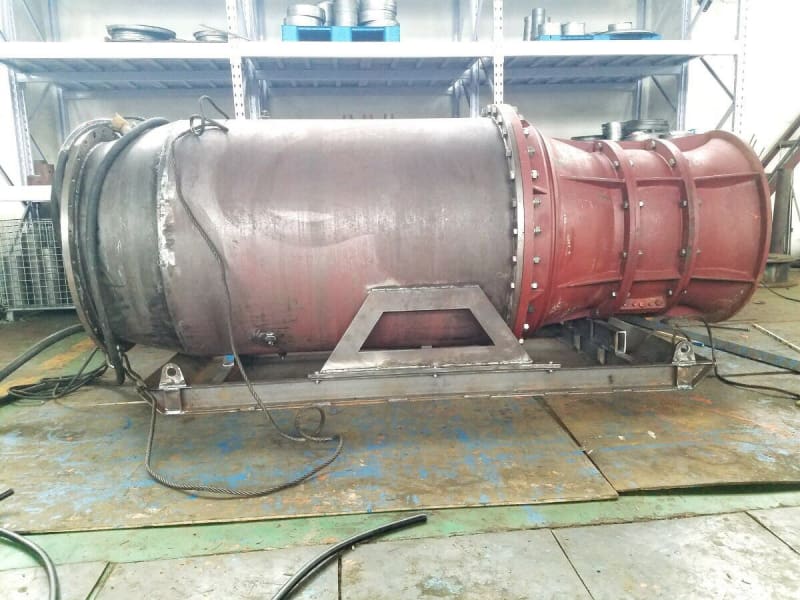
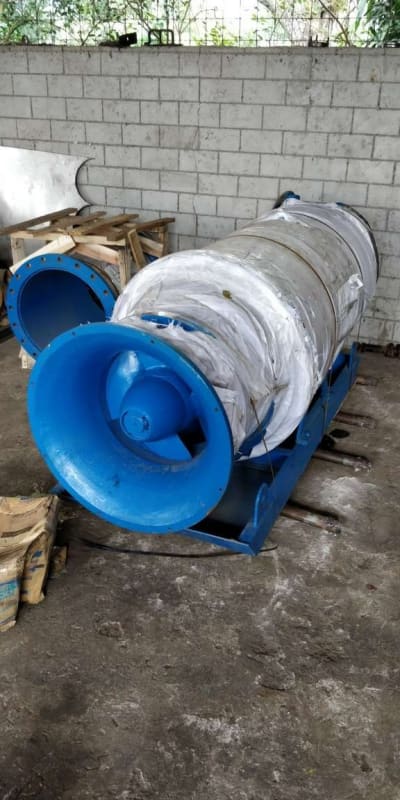
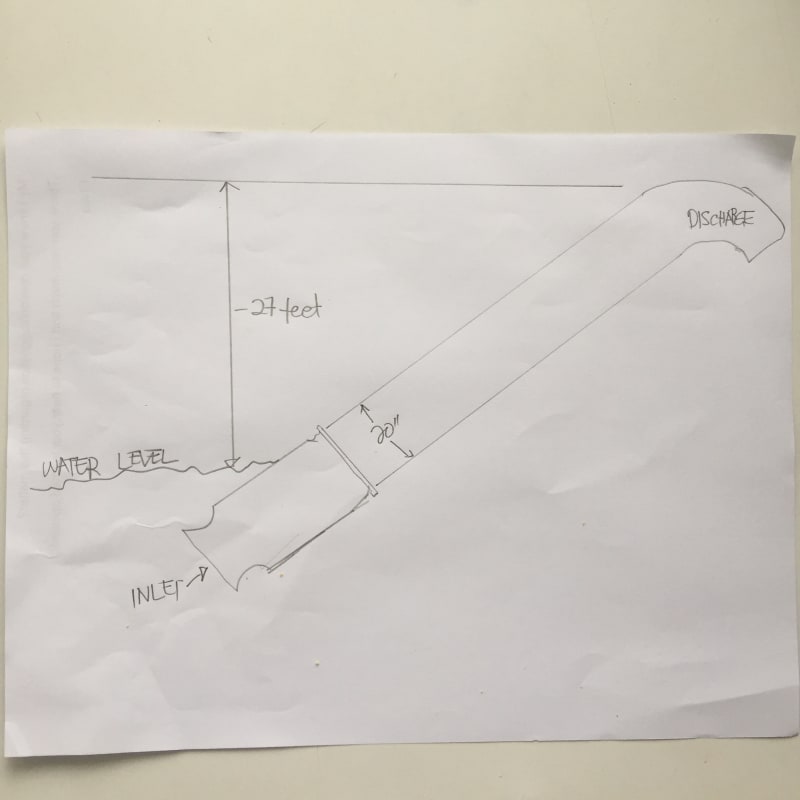
Keith Cress
kcress -