Jharvey2525
Mechanical
- Jul 18, 2019
- 14
I have a rubber hose installed on the discharge of a pump, but its stiffness and flexibility characteristics are unknown. The client prefers these hoses for their wear resistance and ability to reduce both vibration-induced wear on the pump and loads on the nozzles. While these hoses are relatively rigid, they can elongate slightly under pressure.
Given this, I included pressure thrust in my AutoPIPE analysis. Although the pipe stress itself isn't a concern, the load on the discharge pump flange exceeds the allowable limit by about 30%. During operation (60 psig & 95°F), there seems to be pipe lift-off at the top hanger (see attached image), and this additional load appears to be transferring to the pump nozzle.
After discussing with a colleague, he suggested I might be overestimating the impact of pressure thrust. He believes it would be negligible on the pump discharge as most of the thrust would be absorbed by the pump internals. My main concern is the extra piping weight on the pump discharge due to the support lift-off, though I’m questioning if I’m approaching this correctly.
Initially, I considered a spring hanger to mitigate the load during lift-off, but my colleague thinks it's unnecessary. I'm seeking the simplest solution to address this issue without adding a spring hanger, if possible. Please assume the pipe routing will remain the same.
Thank you for your insights.
Given this, I included pressure thrust in my AutoPIPE analysis. Although the pipe stress itself isn't a concern, the load on the discharge pump flange exceeds the allowable limit by about 30%. During operation (60 psig & 95°F), there seems to be pipe lift-off at the top hanger (see attached image), and this additional load appears to be transferring to the pump nozzle.
After discussing with a colleague, he suggested I might be overestimating the impact of pressure thrust. He believes it would be negligible on the pump discharge as most of the thrust would be absorbed by the pump internals. My main concern is the extra piping weight on the pump discharge due to the support lift-off, though I’m questioning if I’m approaching this correctly.
Initially, I considered a spring hanger to mitigate the load during lift-off, but my colleague thinks it's unnecessary. I'm seeking the simplest solution to address this issue without adding a spring hanger, if possible. Please assume the pipe routing will remain the same.
Thank you for your insights.
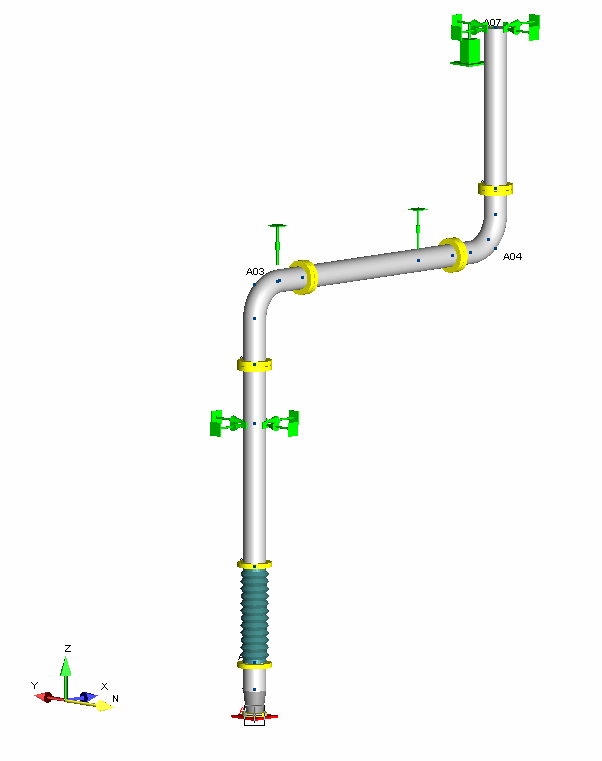