Prometheus21
Mechanical
Hello everyone,
A filling plant is experiencing some issues when mounting fill adapters on the cylinder valves, see illustration image below.
Simply stated: The valve is supplied by another company; we supply the O-ring,connection piece and union nut.
The customer tightens the union nut with 4 Nm, at a rate of 100-800 rpm (automatic installation tool - customer built).
The problem is that approx. 1 in 5 union nuts tends to seize, and require around 20-30 Nm to loosen, requiring the need of a spanner to loosen again.(This happens immediately, no pressurization and/or product usage has been performed yet.) The interesting part is that the customer reports that after the first initial assembly; if one just handtighten the union nut a bit forcefully by hand (no tool, no 150-750 rpm) the nut still seizes and require a spanner to loosen again.
The valve is made of CW617B brass, the connection piece is made out of CW724R brass and the union nut is made out of CW614N brass. The thread in question is W21,80 x 1/14 per DIN 477.
The use of lubricant or anti-seize on the threads are forbidden due to regulations.
My first thought is galling of the threads, and/or other damage to the threads. I am visiting the customer next week and will be checking both the valve and the union nut, and wonder if there is something you guys think I should keep in mind? Anything to look out for in particular? It must be noted that this problem has just recently occured, so I will have to go through the process history and see what could have changed to make this problem appear in the first place.
Thank you for any input you may have.
A filling plant is experiencing some issues when mounting fill adapters on the cylinder valves, see illustration image below.
Simply stated: The valve is supplied by another company; we supply the O-ring,connection piece and union nut.
The customer tightens the union nut with 4 Nm, at a rate of 100-800 rpm (automatic installation tool - customer built).
The problem is that approx. 1 in 5 union nuts tends to seize, and require around 20-30 Nm to loosen, requiring the need of a spanner to loosen again.(This happens immediately, no pressurization and/or product usage has been performed yet.) The interesting part is that the customer reports that after the first initial assembly; if one just handtighten the union nut a bit forcefully by hand (no tool, no 150-750 rpm) the nut still seizes and require a spanner to loosen again.
The valve is made of CW617B brass, the connection piece is made out of CW724R brass and the union nut is made out of CW614N brass. The thread in question is W21,80 x 1/14 per DIN 477.
The use of lubricant or anti-seize on the threads are forbidden due to regulations.
My first thought is galling of the threads, and/or other damage to the threads. I am visiting the customer next week and will be checking both the valve and the union nut, and wonder if there is something you guys think I should keep in mind? Anything to look out for in particular? It must be noted that this problem has just recently occured, so I will have to go through the process history and see what could have changed to make this problem appear in the first place.
Thank you for any input you may have.
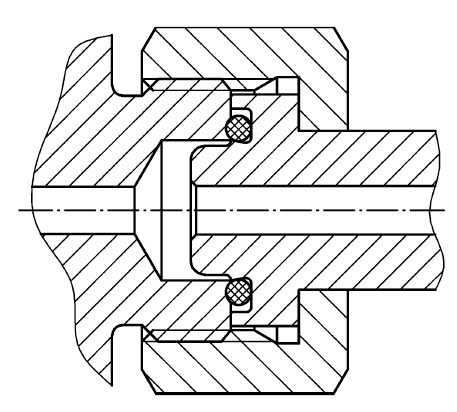