Otibix 1996
Mechanical
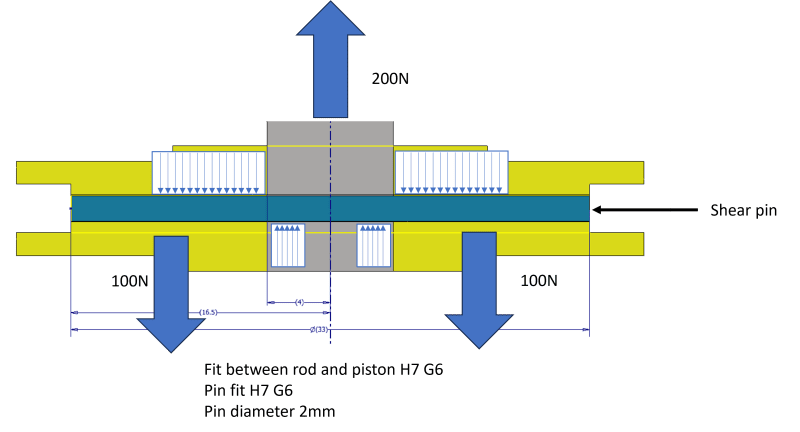
I'm facing a problem trying to assess a shear pin design. The design is made by a third party so we have limited influence but have been asked to ensure the design is fit for purpose.
The design is for a circa - 2mm pin which attaches a 33mm OD pneumatic piston to a 8mm OD piston rod. The pin must be capable of withstanding a design force of 200N but must shear at 500N applied to the piston rod.
The pin was sized accounting for only the shear force and I have been asked to account of bending and bearing stresses in the pin, but seeing as the pin is 33mm long (width of the piston) I am struggling to determine an appropriate moment.
We are working to EN13001-3-1 but this greatly overestimates the force based on the pistons width.
Is there any advice on how to consider this?
FBD