Veer007
Civil/Environmental
- Sep 7, 2016
- 379
Hey guys, i have a situation where my detailer slotted the tube column at base plate due to its larger brace force, however it seems to be wrong as far as i know, has anyone encounter a same situation?
Thanks in advance!!
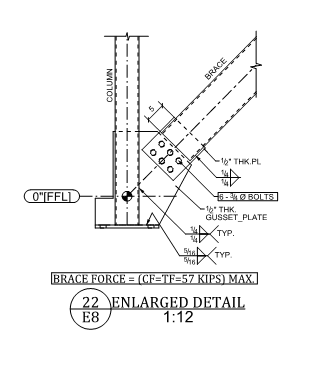
Thanks in advance!!