Hi all. I'm looking at a steel pavilion for a friend and am looking for some confirmation/guidance. I mostly work with wood-framed structures so this easy project is challenging me more than it probably should. As you can see below it is a pavilion with 3 steel a-frames/bents/cranked beams, whatever you want to call them. I have modeled the center one in Risa. It will be built with HSS tubes that weld together at the peak. My sketch below shows the pin and roller supports, the point loads from the purlins that hang into the a-frames, and the reactions at the supports. Here are some questions I have:
- Does my diagram make sense with the pin and roller supports?
- Does the 83 kip-ft moment at the ridge sound reasonable? I don't ever use Risa so I'm not sure I've modeled this correctly.
- How can I show that the full-pen weld at the peak can handle the 83 kip-ft moment?
- Any additional feedback would be appreciated
- Does my diagram make sense with the pin and roller supports?
- Does the 83 kip-ft moment at the ridge sound reasonable? I don't ever use Risa so I'm not sure I've modeled this correctly.
- How can I show that the full-pen weld at the peak can handle the 83 kip-ft moment?
- Any additional feedback would be appreciated
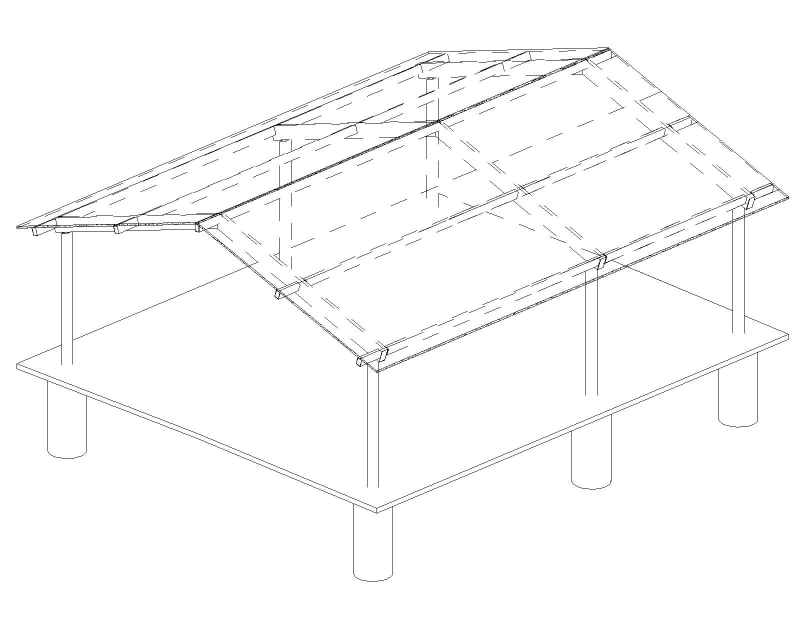
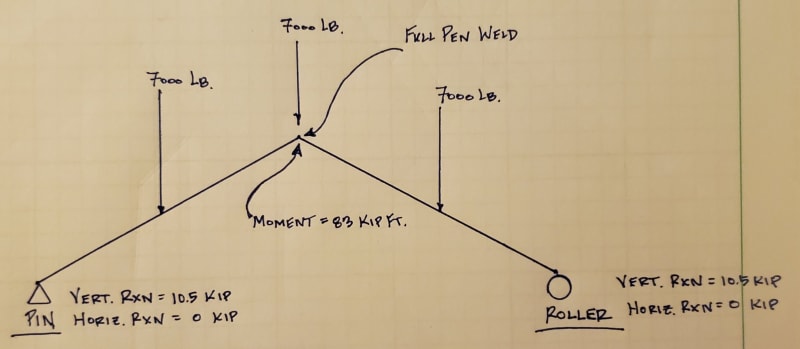