canstruct12
Structural
Hello All,
Canadian structural engineer here. I am currently exploring options to add section capacity to an existing truss. The work would be required to be done in place at ~30feet from the slab below.
The top and bottom chords are T-Sections
Truss Span: 50 feet
Truss Depth: 5 feet
Top Chord: ST 7 WF 30.5
Bottom Chord ST 7 WF 26.5
Web Members: Various Star-Arranged Double Angle Sections (with a single midspan interconnector) 2 - L 3.5 x 3.5 x 5/16 at the truss end to 2 - L 2 x 2 x 1/4 at the truss middle
The truss top chord is proving to be the most difficult to determine a method. It is not possible to add to the top of the T-section without removing the roof and OWSJ. The web members make adding continuous sections to the side or bottom of the T not possible.
Currently exploring welding angles (L4x4x3/4) to the underside of the top chord T. This seems like the only viable option that I can see, due to the physical limitations and interferences. The angle size was chosen to add sufficient area to increase capacity to the required amount, as well fit over the web members and allow weld between the underside of the t-section and angle at the outside.
I am using STAAD Section wizard to determine section properties (STAAD does not give an entirely accurate visual representation of the flange to web radius transition) , then using these to verify sufficient capacity based on applicable CISC S16-19 Standard.
My only concern with this is at the radius transition between the Flange and Web will require chamfering the angle to fit at this location. I was planning to use a 1/4" intermittent weld at 3"-6", and am not sure if there would be enough meat on the angle to effectively weld if it is chamfered to fit.
Any feedback would be appreciated.
Canadian structural engineer here. I am currently exploring options to add section capacity to an existing truss. The work would be required to be done in place at ~30feet from the slab below.
The top and bottom chords are T-Sections
Truss Span: 50 feet
Truss Depth: 5 feet
Top Chord: ST 7 WF 30.5
Bottom Chord ST 7 WF 26.5
Web Members: Various Star-Arranged Double Angle Sections (with a single midspan interconnector) 2 - L 3.5 x 3.5 x 5/16 at the truss end to 2 - L 2 x 2 x 1/4 at the truss middle
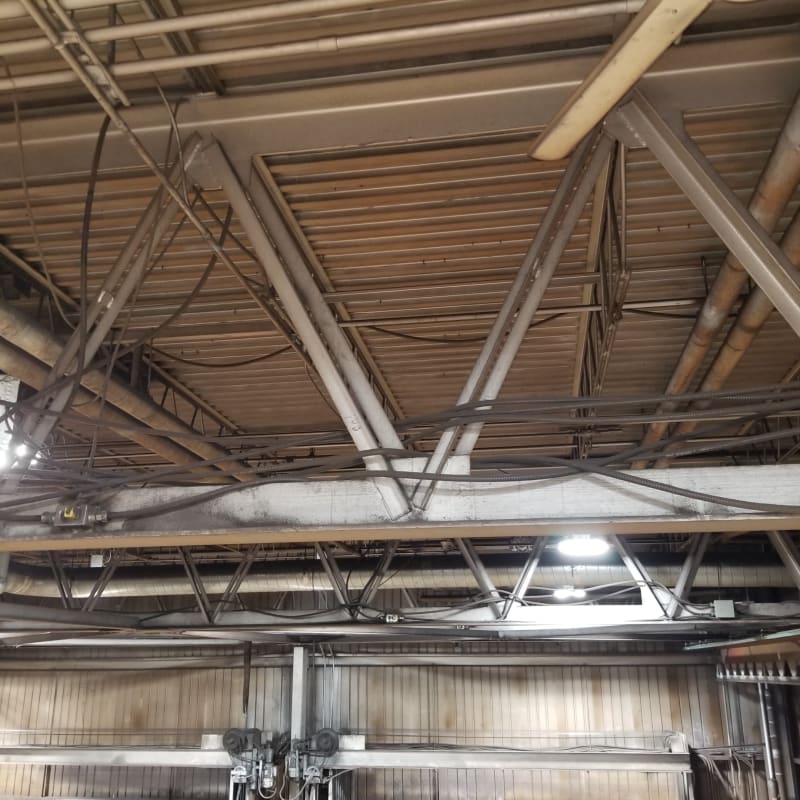
The truss top chord is proving to be the most difficult to determine a method. It is not possible to add to the top of the T-section without removing the roof and OWSJ. The web members make adding continuous sections to the side or bottom of the T not possible.
Currently exploring welding angles (L4x4x3/4) to the underside of the top chord T. This seems like the only viable option that I can see, due to the physical limitations and interferences. The angle size was chosen to add sufficient area to increase capacity to the required amount, as well fit over the web members and allow weld between the underside of the t-section and angle at the outside.
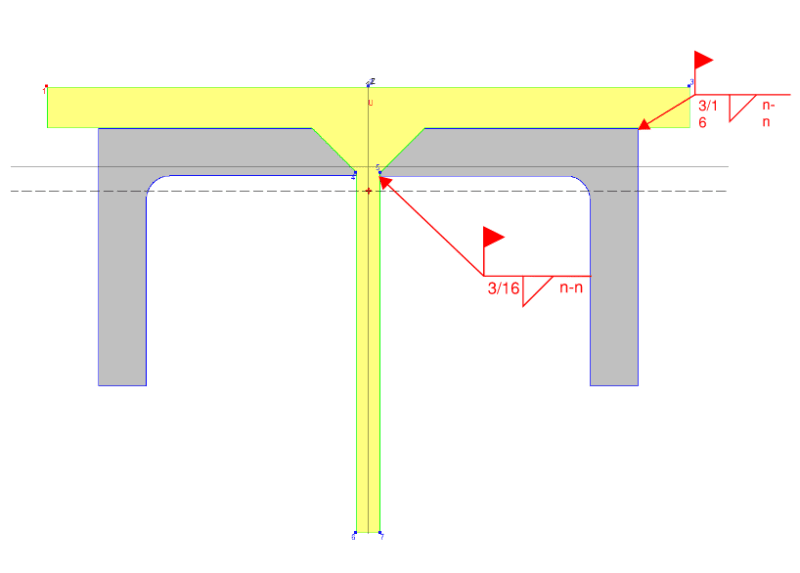
I am using STAAD Section wizard to determine section properties (STAAD does not give an entirely accurate visual representation of the flange to web radius transition) , then using these to verify sufficient capacity based on applicable CISC S16-19 Standard.
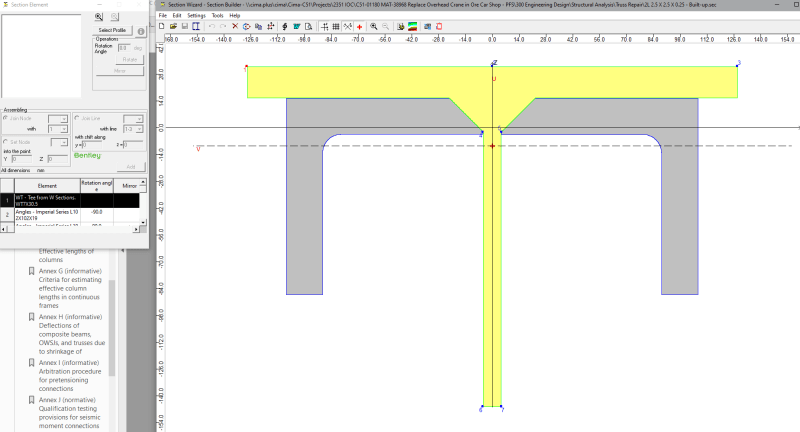
My only concern with this is at the radius transition between the Flange and Web will require chamfering the angle to fit at this location. I was planning to use a 1/4" intermittent weld at 3"-6", and am not sure if there would be enough meat on the angle to effectively weld if it is chamfered to fit.
Any feedback would be appreciated.