Good evening or Good mornign everyone.
I kindly ask your support for a strange case in stress analysis.
Let me describe the problem
I have a condenser with very very low allowable nozzle load.
The external engineer that provide us the stress anlysis in Caesar provide us a strange results.
Due to very very low allowable nozzle load, i kindly ask to them to put an Anchor (Fixed point) next to the nozzle in order to avoid problem.
But the results is different from what i thought, instead to have low value i have a very high value, but for me is strange
Please find here below the configuration, i have the flange attached to the nozzle, an elbow installed to the flange and then a piece of pipe and next to the elbow i will install the pipe shoe welded to the structure.
Please consider that Design pressure is 24 bar(g), and design temperature is 80°C so even very low and the pipe is 3'' with Sch.40 in SA 106 Gr.B
on the flange i have a load of 10'000N on Y direction and even higher on other.
But this value for me is strange and quite difficult to understand
I kindly ask your support for a strange case in stress analysis.
Let me describe the problem
I have a condenser with very very low allowable nozzle load.
The external engineer that provide us the stress anlysis in Caesar provide us a strange results.
Due to very very low allowable nozzle load, i kindly ask to them to put an Anchor (Fixed point) next to the nozzle in order to avoid problem.
But the results is different from what i thought, instead to have low value i have a very high value, but for me is strange
Please find here below the configuration, i have the flange attached to the nozzle, an elbow installed to the flange and then a piece of pipe and next to the elbow i will install the pipe shoe welded to the structure.
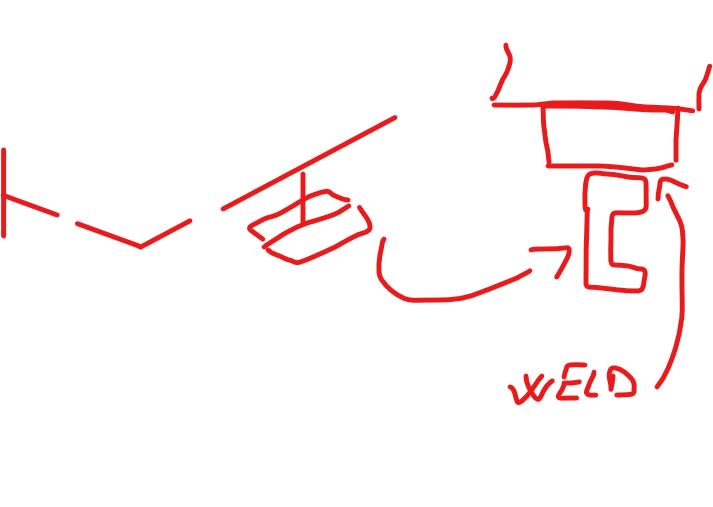
Please consider that Design pressure is 24 bar(g), and design temperature is 80°C so even very low and the pipe is 3'' with Sch.40 in SA 106 Gr.B
on the flange i have a load of 10'000N on Y direction and even higher on other.
But this value for me is strange and quite difficult to understand