I have been a long time lurker on eng-tips and have finally found the need to make a post for myself.
I have recently become familiar with Strut & Tie modeling and am currently faced with designing an offset column attached below. I have tried designing without a drop panel and my tie forces were far too high so added the drop panel in to increase the angle between the strut (black) and the ties (red). I know it would be ideal to have my bottom tie at node C however we do not detail reinforcement in the bottom of our drop panels at our firm.
I am wondering if my current model is reasonable (or even possible) with node B being midway through my strut. Am I missing additional struts or ties? Is this even a Strut & Tie problem or can I use standard methods of analysis? I am having trouble finding the resultant tie forces as I get different results when using the sum of all forces/moments or using simple trig so I'm assuming I am missing elements somewhere.
Any help would be greatly appreciated. Thanks.
I have recently become familiar with Strut & Tie modeling and am currently faced with designing an offset column attached below. I have tried designing without a drop panel and my tie forces were far too high so added the drop panel in to increase the angle between the strut (black) and the ties (red). I know it would be ideal to have my bottom tie at node C however we do not detail reinforcement in the bottom of our drop panels at our firm.
I am wondering if my current model is reasonable (or even possible) with node B being midway through my strut. Am I missing additional struts or ties? Is this even a Strut & Tie problem or can I use standard methods of analysis? I am having trouble finding the resultant tie forces as I get different results when using the sum of all forces/moments or using simple trig so I'm assuming I am missing elements somewhere.
Any help would be greatly appreciated. Thanks.
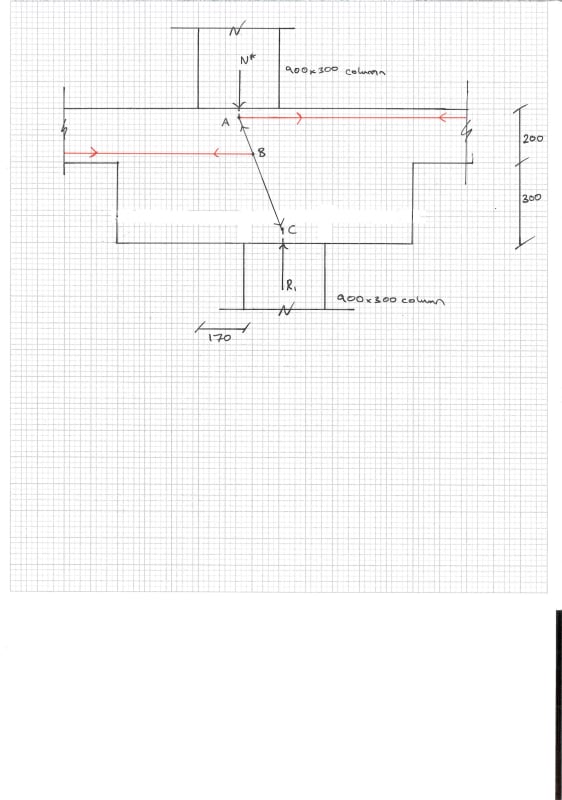