BacBac
Structural
- Aug 11, 2024
- 25
Reviving this thread:
www.eng-tips.com
Does anyone have any ideas on how to justify the starter bars reinforcement is developed at the node?
For the shear ties, reference from Australian Standards, it's said to be fully anchored if shear ties detail is followed (AS3600-2018 clause 12.2.1 that refers back to Clause 8.3.2.4 for anchorage of shear ties).
However, nothing is referred for the development of the starter bars of the column.
Any help would be appreciated
Thanks!.
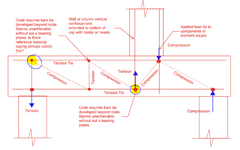
Strut And Tie - Tie Development At Nodes - Structural engineering general discussion
Hi All, Looking for some input on how you all handle ACI requiring tension ties anchorage at nodes. ACI Section 23.8.2 states Tie reinforcement shall be anchored by mechanical devices, post tensioning anchorage devices, standard hooks or straight bar development in accordance with 23.8.3 (Tie...

Does anyone have any ideas on how to justify the starter bars reinforcement is developed at the node?
For the shear ties, reference from Australian Standards, it's said to be fully anchored if shear ties detail is followed (AS3600-2018 clause 12.2.1 that refers back to Clause 8.3.2.4 for anchorage of shear ties).
However, nothing is referred for the development of the starter bars of the column.
Any help would be appreciated
Thanks!.
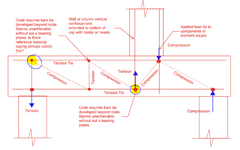