QUESTION
When stud rail studs are fabricated shorter than specified, how short is too short?
CONTEXT
So... post slab pour my contractor tells me that they couldn't get the stud rails that we specified in time and made an unapproved substitution. The substituted studs are an inch short of spec. This is the same project as was discussed in a previous stud rail thread of mine: Link. The two issues are unrelated, however, other than my ongoing concerns for quality control on site. I've included the before and after data below. I've also clipped the ACI 421 sections that deal with stud length (slab depth less covers less a tolerance of half a flexural bar diameter).
My gut tells me this is not a big deal but, being the aye dotter and tee crosser that I am, I call the stud rail supplier to get their take. As with the other thread, they are very permissive. They tell me the short studs are fine. And that's good. They're problem solvers who do their best to make life easy for their customers. Trouble is, I'm just not sure that I buy it. Why don't I buy it? Here's why:
I told the supplier that, if some deficiency in stud length can be deemed acceptable then, logically, there must also be some degree of deficiency in stud length that must be deemed unacceptable. Surely, 2" tall studs at 1" o/c would not be acceptable, right? Clearly there's a bar somewhere that separates the good from the bad. I feel that, to have confidence in this judgment, we ought to know where that bar is. The supplier agreed with this logic but was unable to comment on the position of the bar of acceptability.
My thoughts:
1) The ACI document clips shown below make it clear that, on some level we do care about the height of the studs. The supplier tells me that the only reason for the limitation is that engineers used to try to sandwich the stud heads between layers of tension steel which was goofy.
2) One story of shear reinforcement is this: the shear reinforcement, be it studs or stirrups, should effectively connect the flexural tension and compression zones. In this respect, having the studs terminate lower than the underside of the flexural steel seems as though it would be a problem.
3) Another story of shear reinforcement is this: so long as the reinforcement, be it studs or stirrups, crosses the potential shear cracks and is developed on either side of the cracks, all is well and it doesn't matter if the shear reinforcement makes it to the tensile and compression zones. This is how the stud rail supplier feels about things, particularly given that the studs are not necessarily placed in the same plan location as the flexural steel.
This would lead one to believe that the minimum height of stud would be that required to "develop" the studs either side of the potential shear cracks without initiating a concrete breakout failure below the studs. Per SlideRuleEra's contribution in the other thread, old Nelson stud catalogs indicated that studs needed to be embedded 8-10 stud diameters to preclude breakout. This would lead one to believe that a 6" stud would be the minimum height stud ever.
ORIGINALLY SPECIFIED
- 8" slab
- 6" tall studs (1" cover T&B)
- 4" stud spacing
- 3/8" dia studs
PROVIDED IN FIELD
- 8" slab
- 5" tall studs
- 3" stud spacing
- 1/2" dia studs
- bottom cover maintained.
I like to debate structural engineering theory -- a lot. If I challenge you on something, know that I'm doing so because I respect your opinion enough to either change it or adopt it.
When stud rail studs are fabricated shorter than specified, how short is too short?
CONTEXT
So... post slab pour my contractor tells me that they couldn't get the stud rails that we specified in time and made an unapproved substitution. The substituted studs are an inch short of spec. This is the same project as was discussed in a previous stud rail thread of mine: Link. The two issues are unrelated, however, other than my ongoing concerns for quality control on site. I've included the before and after data below. I've also clipped the ACI 421 sections that deal with stud length (slab depth less covers less a tolerance of half a flexural bar diameter).
My gut tells me this is not a big deal but, being the aye dotter and tee crosser that I am, I call the stud rail supplier to get their take. As with the other thread, they are very permissive. They tell me the short studs are fine. And that's good. They're problem solvers who do their best to make life easy for their customers. Trouble is, I'm just not sure that I buy it. Why don't I buy it? Here's why:
I told the supplier that, if some deficiency in stud length can be deemed acceptable then, logically, there must also be some degree of deficiency in stud length that must be deemed unacceptable. Surely, 2" tall studs at 1" o/c would not be acceptable, right? Clearly there's a bar somewhere that separates the good from the bad. I feel that, to have confidence in this judgment, we ought to know where that bar is. The supplier agreed with this logic but was unable to comment on the position of the bar of acceptability.
My thoughts:
1) The ACI document clips shown below make it clear that, on some level we do care about the height of the studs. The supplier tells me that the only reason for the limitation is that engineers used to try to sandwich the stud heads between layers of tension steel which was goofy.
2) One story of shear reinforcement is this: the shear reinforcement, be it studs or stirrups, should effectively connect the flexural tension and compression zones. In this respect, having the studs terminate lower than the underside of the flexural steel seems as though it would be a problem.
3) Another story of shear reinforcement is this: so long as the reinforcement, be it studs or stirrups, crosses the potential shear cracks and is developed on either side of the cracks, all is well and it doesn't matter if the shear reinforcement makes it to the tensile and compression zones. This is how the stud rail supplier feels about things, particularly given that the studs are not necessarily placed in the same plan location as the flexural steel.
This would lead one to believe that the minimum height of stud would be that required to "develop" the studs either side of the potential shear cracks without initiating a concrete breakout failure below the studs. Per SlideRuleEra's contribution in the other thread, old Nelson stud catalogs indicated that studs needed to be embedded 8-10 stud diameters to preclude breakout. This would lead one to believe that a 6" stud would be the minimum height stud ever.
ORIGINALLY SPECIFIED
- 8" slab
- 6" tall studs (1" cover T&B)
- 4" stud spacing
- 3/8" dia studs
PROVIDED IN FIELD
- 8" slab
- 5" tall studs
- 3" stud spacing
- 1/2" dia studs
- bottom cover maintained.
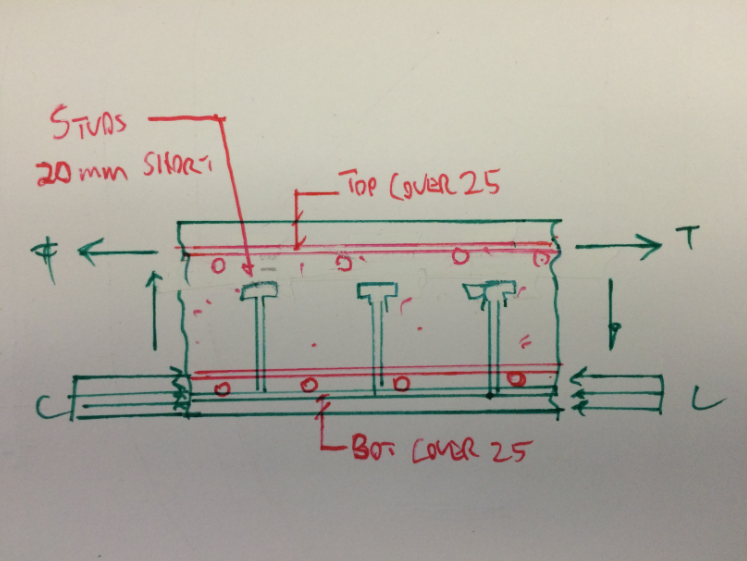
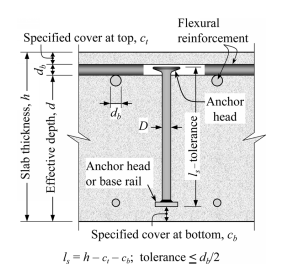
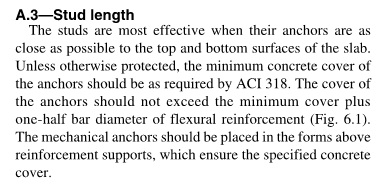
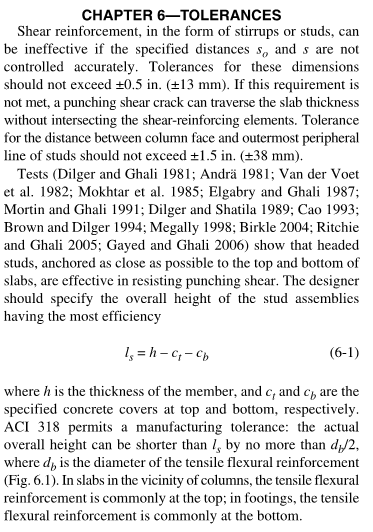
I like to debate structural engineering theory -- a lot. If I challenge you on something, know that I'm doing so because I respect your opinion enough to either change it or adopt it.