MIkkelPoulsen
Mechanical
Hi
I'm having troubles finding out how to calculate a cooling coil system that is submerged in a water tank.
This is what i have of data.
I have a water tank that is filled with none agitated water - this is then is coming in contact with some gasses that makes the water getting up to 70deg C. ¨
This is to hot - so i need to cool this down to under 40 degC.
For this i have available cooling water of 37 degC, so the idea from the process department is to make a cooling coil inside the water tank.
But i'm unsure how to calculate this,
How do i setup a formula so that I can calculate the pipe size and length?
I have the following data:
Tank size: ø1450mm inside
Water volume: 2400L
Water temp: up to 70 deg C
Cooling water temp: 37 degC
Water only has normal conviction - so no moving parts of the water.
I hope somebody has some ideas on formulas or theory i can read on this - i have not made this kind of system before.
I know that it is very inefficient to have the water standing still - but it is not possible right now to get it moving.
But if i make the formulas correct i will be able to calculate the difference if it is agiated or not.
Thanks in advance,
Br
Mikkel
I'm having troubles finding out how to calculate a cooling coil system that is submerged in a water tank.
This is what i have of data.
I have a water tank that is filled with none agitated water - this is then is coming in contact with some gasses that makes the water getting up to 70deg C. ¨
This is to hot - so i need to cool this down to under 40 degC.
For this i have available cooling water of 37 degC, so the idea from the process department is to make a cooling coil inside the water tank.
But i'm unsure how to calculate this,
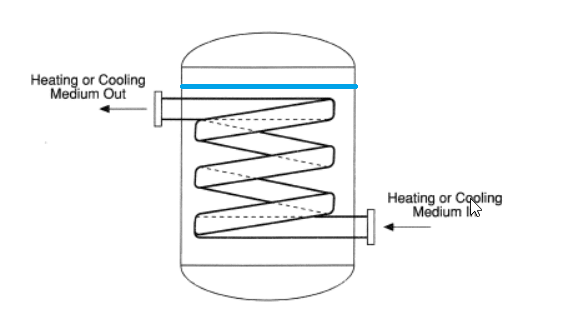
How do i setup a formula so that I can calculate the pipe size and length?
I have the following data:
Tank size: ø1450mm inside
Water volume: 2400L
Water temp: up to 70 deg C
Cooling water temp: 37 degC
Water only has normal conviction - so no moving parts of the water.
I hope somebody has some ideas on formulas or theory i can read on this - i have not made this kind of system before.
I know that it is very inefficient to have the water standing still - but it is not possible right now to get it moving.
But if i make the formulas correct i will be able to calculate the difference if it is agiated or not.
Thanks in advance,
Br
Mikkel