Hello All,
I’m a little stumped the following… any able to offer any insight?
Normal Operating conditions 2x pumps in parallel. Third pump kicks in on level control. When third pump kicks in its flow/current in the middle pump (pump 2) is significantly lower.
Pump 1 & 3 = 40L/s @120A
Pump 2 = 30L/s @100A
If pump 2 is operating under duty conditions it is inline with the other pump (maybe 1-2L/s lower)
I've attached a section view of the pump station, my thoughts is that it needs an inspections to wear ect but I've been told that its always happenened (even other pump i.e. 1 or 3 were doing the same).
I’m a little stumped the following… any able to offer any insight?
Normal Operating conditions 2x pumps in parallel. Third pump kicks in on level control. When third pump kicks in its flow/current in the middle pump (pump 2) is significantly lower.
Pump 1 & 3 = 40L/s @120A
Pump 2 = 30L/s @100A
If pump 2 is operating under duty conditions it is inline with the other pump (maybe 1-2L/s lower)
I've attached a section view of the pump station, my thoughts is that it needs an inspections to wear ect but I've been told that its always happenened (even other pump i.e. 1 or 3 were doing the same).
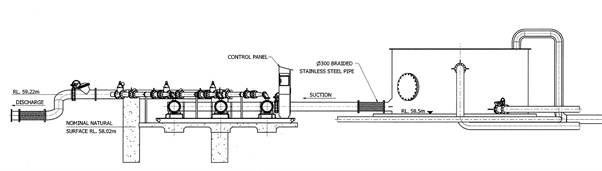