LittleInch
Petroleum
- Mar 27, 2013
- 22,478
A Delta plane appears to have touched a wing tip during landing, ripped the wing off then promptly flipped over onto its back.
As they were on the airfield and this time didn't run into anything or catch fire, everyone is alive, though not surprisingly some injuries.
This video https://www.dailymail.co.uk/news/article-14407855/delta-plane-crash-toronto-fireball-footage.html makes it look like a very hard landing - no visible flare
As they were on the airfield and this time didn't run into anything or catch fire, everyone is alive, though not surprisingly some injuries.
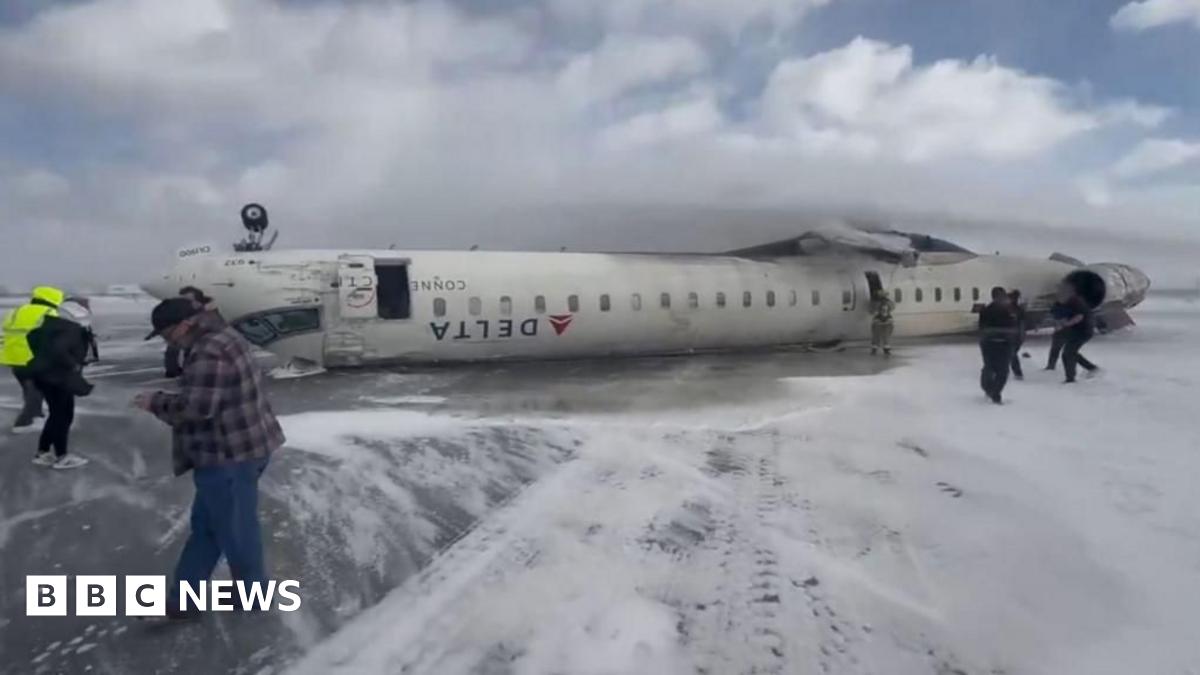
All passengers survive crash landing as plane flips at Toronto airport
Eighteen of the 80 people on board were injured after the Delta plane overturned on landing.
www.bbc.co.uk
This video https://www.dailymail.co.uk/news/article-14407855/delta-plane-crash-toronto-fireball-footage.html makes it look like a very hard landing - no visible flare